Thermoforming is a widely used manufacturing process that involves heating plastic to a pliable...
Types of Injection Molded Plastic Resins: Advantages and Applications
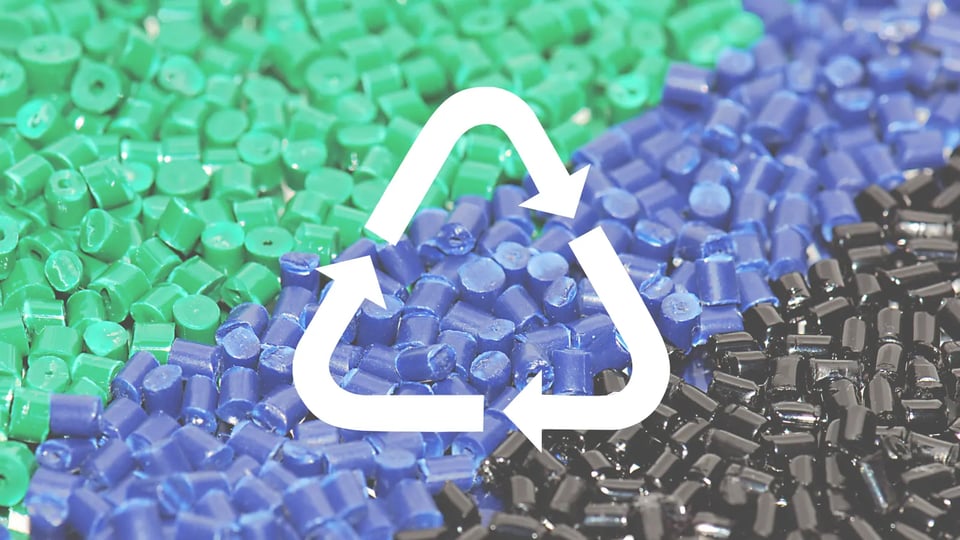
Injection-molded plastic resins are the backbone of countless products we use daily. Each resin boasts unique properties that cater to specific applications, from versatile acrylonitrile butadiene styrene to durable polycarbonate and high-performance nylon.
Understanding the different types of plastic resins, their benefits, and where they excel can be a game-changer for manufacturers and designers seeking the perfect material for their projects.
Common Types of Injection Molded Plastic Resins
Plastic resins are essential in the injection molding process, determining the final product's characteristics, durability, and applications. Let's explore the key types of plastic resins commonly used in injection molding.
Acrylonitrile Butadiene Styrene (ABS)
Acrylonitrile butadiene styrene, commonly known as ABS, is a versatile and widely used thermoplastic polymer that offers a unique combination of properties suitable for various applications.
Common Applications:
- Automotive Components: ABS is used in the automotive industry to manufacture interior and exterior components. These include instrument panels, pillar trims, and bumper grilles, thanks to ABS's durability and impact resistance.
- Consumer Goods: The versatility of ABS makes it a preferred choice for producing consumer goods like computer keyboard components, toys, luggage shells, and household appliance parts. Its ability to be easily shaped and colored adds to its appeal in this sector.
- Medical Equipment: ABS is also used to create various equipment and devices in the medical field. This may include nebulizers, drug delivery systems, compressors, and housings for medical tools.
Polyethylene (PE)
Polyethylene (PE) is a versatile and widely used plastic resin known for its toughness and resistance to abrasion. Here, we explore some typical applications that demonstrate polyethylene's diverse utility in various industries.
Common Applications:
- Packaging: Polyethylene is extensively used in the packaging industry for manufacturing plastic bags, stretch wrap films, and containers due to its durability and flexibility.
- Medical Devices: Medical-grade polyethylene is utilized to create components for medical devices, such as syringes, tubing, and prosthetic devices, owing to its biocompatibility and sterilization capabilities.
- Consumer Goods: Polyethylene is commonly used to produce everyday items like bottles, bins, and toys due to its economical cost and ease of molding.
Nylon (Polyamide, PA)
Nylon, also known as polyamide (PA), is a versatile synthetic polymer with numerous applications across various industries due to its unique properties. Let's delve into some common applications where nylon proves to be a reliable choice:
Common Applications:
- Food Packaging: Nylon films are commonly used in food packaging applications due to their excellent barrier properties, moisture resistance, and puncture resistance.
- Automotive Industry: Nylon is employed in various automotive components for its ability to withstand high temperatures, including engine parts, fuel lines, and interior trim components.
- Consumer Goods: From everyday items like toothbrush bristles and zippers to advanced products like medical equipment housings and sporting goods, Nylon's versatility and durability make it a go-to material for a wide range of consumer goods.
Polycarbonate (PC)
Polycarbonate (PC) is a versatile type of injection-molded plastic resin known for its exceptional properties that make it suitable for various applications. This transparent thermoplastic polymer offers high impact resistance, excellent clarity, and heat resistance, making it ideal for multiple industries.
Common Applications:
- Electronic Components: PCs are commonly found in electrical connectors and housings due to their excellent electrical insulation properties and heat resistance.
- Automotive Industry: With its impact resistance and lightweight properties, PC is extensively utilized in the automotive sector. Applications include headlight lenses, interior components, dashboard panels, etc.
- Medical Equipment: Polycarbonate is vital in the medical field for manufacturing surgical instruments, drug delivery systems, hemodialysis membranes, blood reservoirs, and blood filters.
- Safety Gear: Polycarbonate is used in safety helmets, face shields, and protective goggles due to its exceptional impact resistance.
- Construction Materials: Polycarbonate is favored in the construction industry for roofing, glazing, and skylight applications.
Polypropylene (PP)
Polypropylene (PP) is a versatile thermoplastic polymer widely used in various industries due to its beneficial properties. Let's explore some applications where polypropylene excels:
Common Applications:
- Packaging: One of the primary uses of polypropylene is in packaging materials. Its durability and resistance to moisture make it an ideal choice for packaging products ranging from food items to consumer goods.
- Automotive Industry: Polypropylene has extensive applications in the automotive sector. Due to its lightweight nature and strength, it is used to manufacture vehicle interior parts such as bumpers, dashboard trims, and door panels.
- Medical Devices: Polypropylene is also commonly used in the medical field to produce medical devices and components. Its sterilization resistance makes it suitable for applications requiring hygienic materials.
Polyoxymethylene (POM)
Polyoxymethylene (POM), or acetal, is a versatile engineering thermoplastic with excellent mechanical properties. It is widely used in various industries due to its high stiffness, low friction, and excellent dimensional stability.
Common Applications:
- Automotive Industry: POM is commonly used in the automotive sector for fuel system components like fuel caps, fuel filler necks, and fuel sender units due to its chemical resistance and durability.
- Electrical and Electronic Applications: Its excellent electrical insulation properties make POM valuable in electrical and electronic applications where insulation and resistance to moisture are crucial.
- Medical Devices: The medical industry benefits from POM's biocompatibility and resistance to various chemicals, making it suitable for applications like surgical instruments, dental components, and drug delivery devices.
Thermoplastic Elastomer (TPE)
Thermoplastic elastomers (TPEs) are versatile materials known for their unique elastomeric and thermoplastic properties. TPEs exhibit excellent flexibility, resilience, and durability, making them ideal for various applications across different industries.
Common Applications:
- Automotive Industry: TPEs are widely used in automotive applications such as weather seals, gaskets, and interior components due to their flexibility and resistance to harsh environmental conditions.
- Medical Devices: TPEs are utilized in the medical field to manufacture components like tubing, syringe tips, and seals due to their biocompatibility and ease of sterilization.
- Consumer Goods: TPEs find applications in consumer products like grips, handles, and sporting goods due to their soft-touch feel and impact resistance.
Thermoplastic Polyurethane (TPU)
Thermoplastic polyurethane (TPU) is a versatile material known for its exceptional properties that make it suitable for various applications across different industries. TPU combines the best features of plastic and rubber, offering flexibility, durability, and resistance to abrasion and chemicals.
Common Applications:
- Footwear: TPU is commonly used in the footwear industry due to its flexibility and durability. It can be found in shoe soles, straps, and waterproof shoe coatings.
- Sports Equipment: TPU's impact resistance and tear strength make it ideal for sports equipment such as protective gear, padding, and sports shoe components.
- Medical Devices: TPU's biocompatibility and flexibility make it a suitable material for medical tubing, catheters, and prosthetic components.
Unique Material Blends
Vantage Plastics partakes in heavy research and development and has the capability to utilize unique blends of materials. We offer proprietary solutions that are only available here. Our innovative approach includes integrating additives like Carbon Fiber for strength, Calcium Carbonate for durability, Talc for fire retardancy, and CS-320 for conductivity, further demonstrating our commitment to innovatively responsible solutions in thermoforming and injection molding.
One of our proprietary solutions is VanTech, an injection-moldable and thermoformable material that has advantages over TPU. VanTech boasts anti-chafing properties and anti-skid benefits and is engineered to safeguard sensitive products during transit and handling, unlocking significant long-term cost savings for our customers. When used in thermoforming with HDPE, it does not need to be removed like TPU before recycling.
Vantage Plastics is dedicated to sustainability, sourcing materials from waste streams and exploring reclaimed ocean plastics for injection molding. Our efforts not only reduce waste but also combat global warming.
Advantages of Injection Molded Plastic Resins in Manufacturing
Injection molding offers various advantages, making it a popular choice in manufacturing processes. Here are some key benefits:
Cost-Effectiveness
One of the significant advantages of injection molding is its low cost per part. The ability to create complex shapes and designs with precision reduces the need for additional machining, trimming, or finishing operations, contributing to cost savings.
Precision and Detail
The injection molding process allows for intricate and detailed parts with tight tolerances. This level of precision ensures consistency in product quality and performance.
Low Waste
Injection molding generates minimal waste compared to traditional manufacturing methods. The ability to recycle excess plastic and regrind scrap material reduces environmental impact and enhances sustainability.
Explore Our Injection Molding Capabilities
Thanks to cutting-edge techniques and materials, the engineering teams at Vantage Plastics and LOTIS Technologies have become experts in returnable dunnage and packaging solutions. Our collaboration has led to significant advancements in injection-molded returnable dunnage, resulting in efficient, cost-effective, and environmentally friendly packaging solutions. LOTIS technologies specializes in crafting custom solutions such as shipping trays, rack dunnage, and automated pallets, including unique offerings like stacking columns.
Contact us today to learn more about how Vantage Plastics and LOTIS Technologies can bring your project to market.