Thermoforming vs. Injection Molding
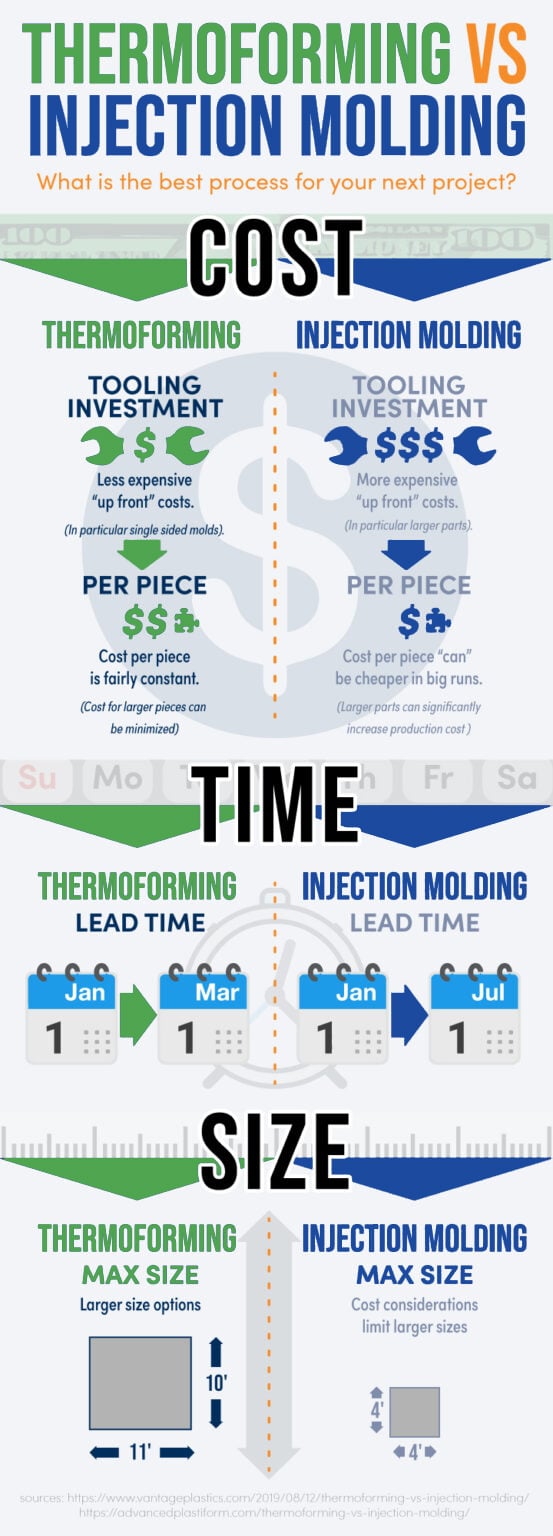
What's the Difference?
The differences and similarities between thermoforming and injection molding is a question we get a lot. Someone comes to us with a project, trying to understand the two processes. Both are popular manufacturing processes for producing plastics parts. While thermoforming is generally used for large designs and smaller production runs, injection molding tends to be used for small intricate parts and large production runs. Here’s some brief descriptions between the two processes.
Tooling
In the tooling phase of thermoforming a single 3D form is created out of aluminum, wood, polyurethane or a 3D printer. In injection molding, a double-sided 3D mold is made from aluminum, steel, or beryllium-copper alloy. There is an advantage in timing and price with thermoforming since prototype samples can be made from CNC cut wood tooling. Tooling costs for large product tooling is substantially less with thermoforming.
Materials
Thermoforming can use a variety of different materials to create the flat sheets that get molded into the product. There are options for a different finish, color, and thickness of the product. Injection molded products use thermoplastic pellets, that are available in a wide variety of materials and colors as well.
Production
In thermoforming, a flat sheet of plastic is heated to a pliable temperature, then molded to the tool’s shape using suction from a vacuum or both suction and pressure. In injection molding, plastic pellets are heated to a liquid state and injected into the mold.
Finishing
The final pieces of the thermoformed product are trimmed, then can be used uncoated, or painted, silk-screened or have specialty coatings applied. The final pieces of the injection molded product are removed from the mold where they are commonly painted for aesthetic reasons. They can also be silk-screened or have specialty coatings.
Thermoforming
Injection Molding
Time
With the combination of tooling and production, it can give an accurate measurement on the amount of time it takes to manufacture your products. In thermoforming, the average time for tooling is 0-8 weeks. Following tooling, production usually occurs within 1-2 weeks after the tool is approved. With injection molding, tooling takes 12-16 weeks and can be up to 4-5 weeks after when production starts.
Cost
The cost of tooling in thermoforming is much cheaper than the cost of injection molding. However, the cost of production per piece in injection molding can be less expensive than thermoforming. Typically, plastic injection molding is used for large, high-volume production runs and thermoforming is used for smaller production quantities as well as large production runs.
Whether you’re working with plastic pellets for injection molding or sheets of plastic for thermoforming, both methods create great reliability and high quality. The best option for a specific project depends on the unique requirements of the application at hand.
Vantage Plastics + Lotis Technologies
Vantage Plastics has several thermoforming machines including one of the largest in the world. This machine is capable of running production with multiple tools at the same time which allows us to be competitive with injection molding when large volume, large product production runs are required. We have also partnered with Lotis Technologies to offer injection molded products. This team up allows to provide our customers with the best option for their needs.
Ready to elevate your manufacturing processes?
The engineering teams at Vantage Plastics and Lotis Technologies, have developed expertise in returnable dunnage and packaging solutions, integrating cutting-edge techniques and materials into their design and manufacturing processes. This highly integrated team has led to significant advancements in injection-molded returnable dunnage, creating efficient, cost-effective, and environmentally friendly packaging solutions. These developments are particularly notable in the context of the growing trend towards automation in the dunnage industry, driven by the need to improve efficiency, reduce errors, and lower costs. Contact us today to discover how we can transform your production with our expert services.