Thermoset vs Thermoplastics: What’s the Difference?
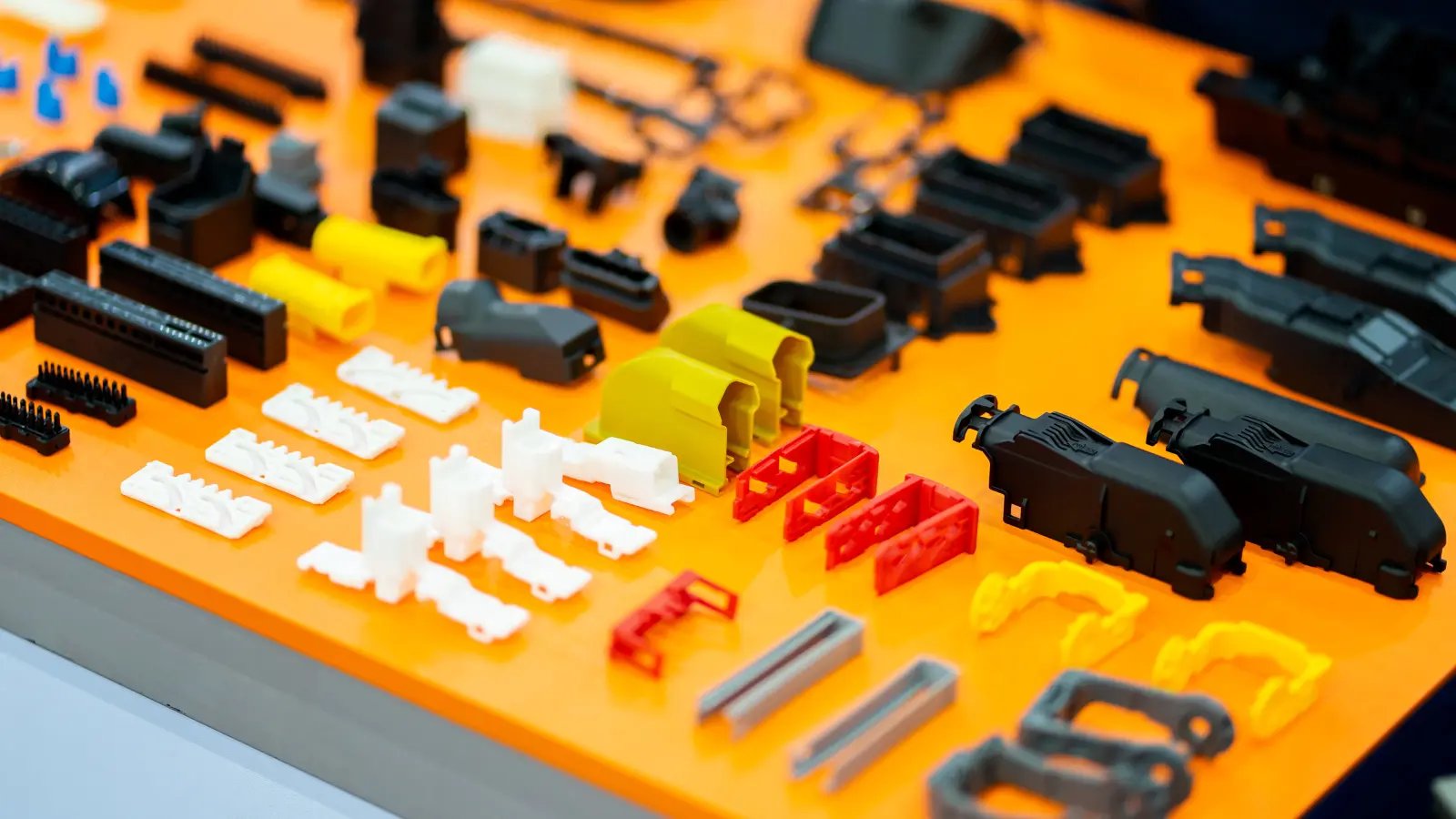
Exploring Thermoset Plastics
Thermoset plastics undergo an irreversible curing process, transforming from liquid into hardened, insoluble, and infusible material. Thermoset products are usually processed through various methods, including injection molding, compression molding, or transfer molding.
Once thermoset plastics are cured, they retain their shape and cannot be reshaped or reformed, making them ideal for applications requiring durability and heat resistance where many other plastics would fail.
During the curing process, thermoset plastics are subjected to heat or radiation, causing the polymer chains to undergo a chemical reaction known as cross-linking. This process creates a three-dimensional network of interconnected polymer chains, resulting in a rigid and stable structure that cannot be softened or reshaped upon reheating. Examples of thermoset materials include epoxy resins, phenolic resins, and polyurethanes, which are widely used in various industries due to their unique properties.
Thermoset Plastic Applications and Industries
Thermoset materials offer numerous benefits for manufacturers, including the ability to create durable and long-lasting products that can withstand harsh operating conditions. Industries such as aerospace, electrical, and appliance manufacturing rely on thermoset plastics for their exceptional heat-resistant and durable properties.
In the aerospace industry, thermoset composites are utilized in aircraft components due to their high strength-to-weight ratio, corrosion resistance, and ability to withstand elevated temperatures. Electrical applications, such as insulating components and circuit boards, benefit from thermoset plastics' electrical insulating properties and flame resistance. Additionally, thermoset plastics are widely employed in appliance manufacturing for their heat-resistant characteristics, making them suitable for components subjected to elevated temperatures within household appliances.
Pros of Thermoset Plastics
- Good chemical resistance
- Superior heat resistance at high temperatures
- Strong dimensional stability
- High Strength, toughness, and rigidity
- Moldability with different tolerances
- Flexible product design and aesthetic finishes
- Water and Corrosion resistance
Cons of Thermoset Plastics
- Non-Recyclable
- Can’t be remolded or reshaped
- More difficult to surface finish
Understanding Thermoplastics
Thermoplastics are a class of polymers that become pliable or moldable when heated and solidified upon cooling. Thermoplastics are commonly processed using methods such as injection molding, extrusion, blow molding, and thermoforming. The unique molecular structure of thermoplastics sets them apart from other types of plastics, making them widely used in various industries.
The molecular structure of thermoplastics consists of long polymer chains that lack a cross-linked structure. Unlike thermoset plastics, thermoplastics can be repeatedly melted, reshaped, and recycled without significantly altering their properties. Common examples of thermoplastic materials include polyethylene (PE), polypropylene (PP), polystyrene (PS), polyvinyl chloride (PVC), and polyethylene terephthalate (PET). The ability of thermoplastics to undergo reversible changes upon heating and cooling makes them suitable for a wide range of applications.
Thermoplastic Applications and Industries
Thermoplastics offer several advantages for manufacturers, including ease of processing, reduced production costs, and the ability to create complex shapes. The recyclability of thermoplastics also aligns with sustainable production practices, appealing to environmentally conscious consumers and regulatory standards.
Thermoplastics find application across various industries due to their exceptional versatility. In the automotive industry, they are extensively used for manufacturing components such as bumpers, interior panels, and dashboards due to their lightweight nature and durability. Thermoplastics are widely utilized in packaging for their impact resistance and ability to be molded into various shapes for different products. Thermoplastics are common for pipelines, insulation, and roofing materials in the construction sector, providing strength and resilience. Additionally, in the consumer goods industry, they can be found in everyday products like bottles, toys, and kitchenware due to their cost-effectiveness and flexibility.
Pros of Thermoplastics
- Can be easily remolded and reshaped
- Can be recycled
- High impact and corrosion resistance
- Extremely adhesive to metal
- Anti-slip enhancement properties
- Detergent and chemical resistance
- Flexibility and elongation of the coating film
- Good electrical insulation
- Aesthetically superior finishes
Cons of Thermoplastics
- May soften or deform under high temperatures, limiting their use in applications requiring heat resistance.
- May not have the same level of structural integrity as thermoset plastics
- Typically more expensive than thermosetting polymers
Thermoset vs. Thermoplastic Environmental Impact
Manufacturers increasingly consider environmental aspects when choosing between materials for their products. With their remoldable nature, thermoplastics contribute to streamlined production processes, as they can be melted and reformed multiple times without significant degradation. Additionally, this reusability minimizes material waste, aligning with sustainable manufacturing practices.
In contrast, although recycling thermoset plastics on a large scale is challenging, if not impossible, their durability and heat resistance often lead to longer product lifespans, helping reduce the overall environmental footprint of manufacturing processes.
Partner With Us for Thermoset Plastic and Thermoplastic Solutions
Vantage Plastics is an experienced plastics processor with expertise in working with thermoset plastic and thermoplastic materials for various project requirements. Our expertise in thermoforming allows for the creation of intricate shapes and precise designs, and our injection mold making capabilities ensure the production of high-precision components with efficiency and accuracy. Contact Vantage Plastics today to explore how their expertise can elevate your projects.