Plastic thermoforming is a versatile manufacturing process that has revolutionized the production...
Types of Thermoplastic Resins: Advantages and Applications
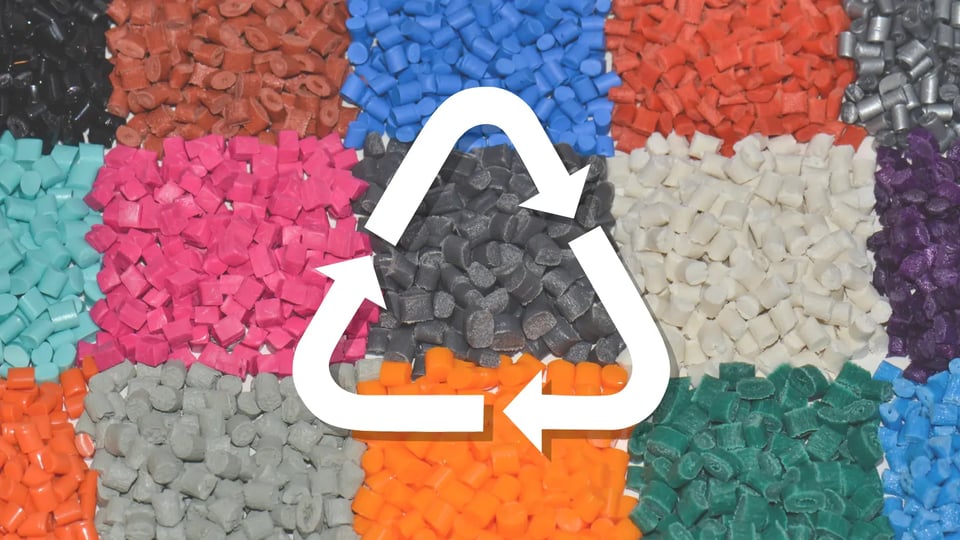
Thermoforming is a widely used manufacturing process that involves heating plastic to a pliable forming temperature, shaping it into a specific form, and trimming it to create a usable product. The choice of which type of plastic resin is crucial in this process, as it directly impacts the characteristics and performance of the final product.
Thermoplastic resins offer various characteristics and applications, making them integral to numerous industries and products we encounter daily. Each type of resin brings its own set of advantages, allowing manufacturers to tailor their material selection to meet specific product requirements. At Vantage Plastics and our Lotis Technologies injection molding business unit, we also develop unique blends of thermoplastics to solve unique issues that are often encountered.
Common Types of Thermoplastics Used in Thermoforming
When it comes to thermoforming, various types of thermoplastics play a crucial role in shaping the products around us. Explore some of the diverse applications that highlight the adaptability of plastic resins in thermoforming processes.
HMWPE (High Molecular Weight Polyethylene)
HMWPE is a durable and cost-effective resin widely used in plastic thermoforming for its superior impact resistance, chemical resistance, and ease of processing. It finds applications in diverse industries such as automotive, industrial, and chemical processing.
Common Applications:
- Plastic pallets: HMWPE's superior impact resistance is ideal for durable and robust plastic pallets.
- Automotive parts: Its toughness and durability make HMWPE suitable for various automotive components.
- Industrial containers: HMWPE's resilience is valuable for industrial containers.
- Recreational equipment: HMWPE's ability to endure heavy blows makes it a preferred choice for recreational equipment.
HDPE (High-Density Polyethylene)
HDPE's strength, moisture resistance, and FDA approval make it a go-to material for packaging, healthcare products, and industrial applications. Its ability to withstand various environmental factors and aggressive substances makes it an excellent choice for multiple products.
Common Applications:
- Bottles and containers: HDPE's lightweight and flexible nature makes it a preferred choice for bottles and containers.
- Chemical processing equipment: The material's excellent chemical resistance makes it suitable for various chemical processing applications.
- Storage tanks and pipework: HDPE's durability and corrosion resistance contribute to its use in storage tanks and pipework.
ABS (Acrylonitrile Butadiene Styrene)
ABS is prized for its impact resistance, heat stability, and sleek surface finish. These qualities make it a top choice for electronic housings, automotive components, and recreational equipment, where durability and an attractive appearance are essential.
Common Applications:
- Automotive components: ABS is commonly used in interior and exterior automotive components for its strength and impact resistance.
- Plastic toys: Its versatility and durability make ABS a popular choice for toy manufacturing, like LEGO’s.
- Consumer electronics housings: ABS's aesthetic appeal and durability contribute to its use in consumer electronics.
TPU (Thermoplastic Urethane)
Thermoplastic Urethane (TPU) is a versatile material with numerous benefits. It is highly flexible, durable, and resistant to abrasion, making it suitable for applications like athletic shoes and industrial components. With resistance to UV radiation, TPU excels in outdoor settings.
Common Applications:
- Footwear: TPU's flexibility and durability make it suitable for athletic shoes and other footwear applications.
- Medical tubing: TPU's biocompatibility and flexibility contribute to its use in medical tubing.
TPO (Thermoplastic Olefin)
Thanks to its weather and impact resistance, TPO combines the characteristics of rubber with the processability of plastic, making it a preferred material for automotive parts, roofing materials, and various other outdoor applications.
Common Applications:
- Automotive interiors: TPO is commonly used for dashboards and door panels in automotive interiors.
- Roofing membranes: Its weather resistance makes TPO suitable for roofing membranes.
- Industrial applications: TPO's durability and chemical resistance contribute to its use in various industrial applications.
PS (Polystyrene)
Polystyrene (PS) offers a range of benefits, including its lightweight nature, versatility for molding into various shapes, and cost-effectiveness, making it a popular choice for disposable packaging and insulation in construction. PS is hygienic, provides thermal insulation, and is resistant to moisture.
Common Applications:
- Disposable packaging: PS's lightweight nature makes it suitable for disposable packaging, including cups, trays, and food containers.
- Insulation: PS is used for insulation in construction.
PC (Polycarbonate)
Polycarbonate is valued for its exceptional impact resistance and optical clarity. It is a popular choice for products ranging from safety goggles and electronic display screens to bulletproof glass and medical devices.
Common Applications:
- Eyewear lenses: PC's optical clarity makes it suitable for eyewear lenses.
- Compact discs: Its durability and optical properties are valuable for compact disc manufacturing.
- Safety helmets: Polycarbonate's impact resistance makes it an ideal material for safety helmets.
- Medical devices: PC is used in medical devices due to its transparency, biocompatibility, and sterilizability.
PMMA (Polymethyl-methacrylate) (Acrylic)
Polymethyl-methacrylate (PMMA), or Acrylic, offers a range of benefits, including exceptional clarity and transparency, weather resistance, lightweight nature, impact resistance, versatility in design, ease of fabrication, biocompatibility, chemical resistance, aesthetic appeal, and recyclability.
Common Applications:
- Windows and Skylights: Acrylic's transparency and weather resistance make it suitable for window applications.
- Aquariums: PMMA's clarity and impact resistance contribute to its use in aquariums.
- Dental Applications: This includes creating artificial teeth, denture bases, dentures, obturators, orthodontic retainers, temporary crowns, and repairing dental prostheses.
Advantages of Thermoplastics in Manufacturing
The numerous types of thermoplastics offer many advantages, making thermoforming a popular choice for various manufacturing applications.
Design Flexibility
Thermoplastics provide unparalleled design flexibility, allowing manufacturers to create intricate shapes, textures, and custom designs with thermoforming. This versatility makes them ideal for producing complex and aesthetically appealing products that meet specific customer requirements.
Cost-Efficiency
One of the significant advantages of thermoforming plastic resins is their cost-effectiveness. The manufacturing process involves minimal tooling and setup costs, making it a more economical option for both small-scale and large-scale production runs. Additionally, the lightweight nature of thermoplastics helps reduce shipping and handling expenses.
Recyclability and Sustainability
Many plastic resins used in thermoforming processes are known for their recyclability and sustainability, aligning with the growing demand for eco-friendly manufacturing practices. These resins can be easily recycled and reused, reducing the environmental impact while promoting a circular economy. Manufacturers can contribute to sustainable production and reduce their carbon footprint by utilizing various types of thermoplastics in thermoforming processes.
Quality Thermoplastic Materials Matter at Vantage Plastics
At Vantage Plastics, quality materials are paramount. Our objective is to offer customized solutions to customers by leveraging an extensive range of materials, including standard thermoplastic commodities and exclusive plastic blends. Our innovation extends to the integration of additives such as Carbon Fiber, Calcium Carbonate, Talc, and CS-320, providing diverse benefits.
Our commitment to customization is reflected in the ability to create products in any color of your preference. Moreover, we provide the option of incorporating colored stripes, not only improving visibility but also adding a personalized touch to fulfill your specific requirements. Contact Vantage Plastics today to learn more.