The Power of Thermoforming Automotive Plastic Parts
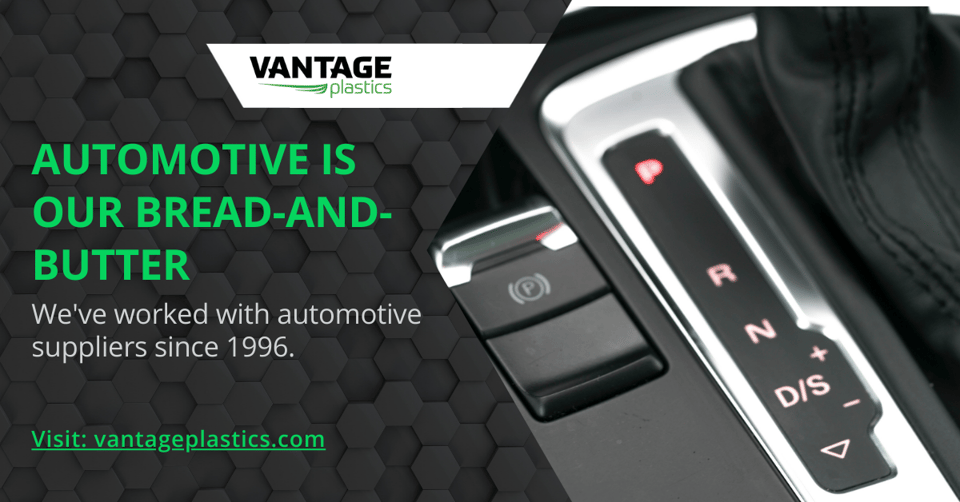
WHY PLASTIC IS VITAL IN THE AUTOMOTIVE INDUSTRY
Plastics have transformed the automotive industry by offering a plethora of benefits. Plastic thermoforming enables manufacturers to create fuel-efficient vehicles with enhanced safety features while simultaneously reducing production costs and minimizing environmental impact. The ability to design parts using thermoformed plastics has opened up new avenues for ongoing innovation and creativity in the automotive industry.
Common plastic parts that can be manufactured using thermoforming in the automotive industry include:
- Bumpers: Thermoforming allows for the production of lightweight and impact-resistant bumpers that contribute to vehicle safety.
- Door Panels: Thermoformed door panels offer design flexibility, durability, and resistance to weathering.
- Dashboard Components: Thermoforming enables the creation of intricate and customized dashboard components that are both visually appealing and functional.
- Insulation Materials: Thermoformed insulation materials contribute to noise reduction and temperature control within the vehicle cabin.
- Grilles: Thermoformed grilles provide a lightweight and stylish option while maintaining the required strength and durability.
- Body Panels: Thermoforming enables the production of lightweight body panels that contribute to overall fuel efficiency and performance.
- Engine Covers: Thermoformed engine covers offer heat resistance and protection while reducing vehicle weight compared to traditional materials.
ADVANTAGES OF AUTOMOTIVE THERMOFORMING
Apart from being lightweight, thermoformed plastic parts offer numerous advantages over traditional metals in the automotive industry. The benefits of thermoforming automotive parts include:
- Safety Enhancements: Impact-resistant plastic parts provide excellent strength-to-weight ratios, contributing to safer vehicle components. Thermoformed automotive parts obtain high heat resistance and flame retardancy, an imperative feature for the vehicle market.
- Weight Savings: Replacing heavier metal parts with lightweight plastics significantly improves a vehicle’s fuel economy. By reducing overall vehicle weight, lightweight plastics contribute to better performance, ideal for both fuel and electric vehicles (EV) in regards to energy efficiency.
- Minimal Corrosion Damage: Unlike metals, most plastics are resistant to rust and corrosion, extending the lifespan of vehicle parts and reducing maintenance costs.
- Reduced Energy Consumption: Plastic manufacturing processes typically require less energy than metalworking techniques, contributing to a more sustainable production cycle. Additionally, many plastic polymers are recyclable, making them a more environmentally friendly option for automotive manufacturing.
- Moldability and Design Flexibility: The moldability of plastics allows for alternative creativity and innovation in vehicle design. Manufacturers can easily create complex shapes and intricate designs using plastic thermoforming.
- Cost-Efficiency: The blend of quality and affordability in thermoforming automotive parts makes it a cost-effective choice. Using plastic materials often results in lower production costs and reduced energy consumption during the manufacturing process.
THE FUTURE OF DEMAND IN AUTOMOTIVE THERMOFORMING
The future of plastic thermoforming in the automotive industry looks promising. With an increasing demand for plastic components, driven by the rise of electric vehicles (EVs), underscores the importance of plastic thermoforming in shaping the future of transportation.
As technology progresses, we can expect further advancements in plastic materials and manufacturing processes, opening up new possibilities for innovation and sustainability in the automotive industry.
NEED MATERIAL SOLUTIONS FOR YOUR AUTOMOTIVE NEEDS?
Partnering with a reliable plastic thermoforming provider, such as Vantage Plastics, allows manufacturers to select the right plastic for their automotive manufacturing solutions. Contact Vantage Plastics today to explore their range of custom automotive thermoforming solutions and unleash the full potential of thermoformed plastics in your manufacturing process.