Thermoformed plastic, a widely used material in various industries, has raised concerns regarding...
Metal vs. Plastic: The Benefits of Thermoformed Plastics
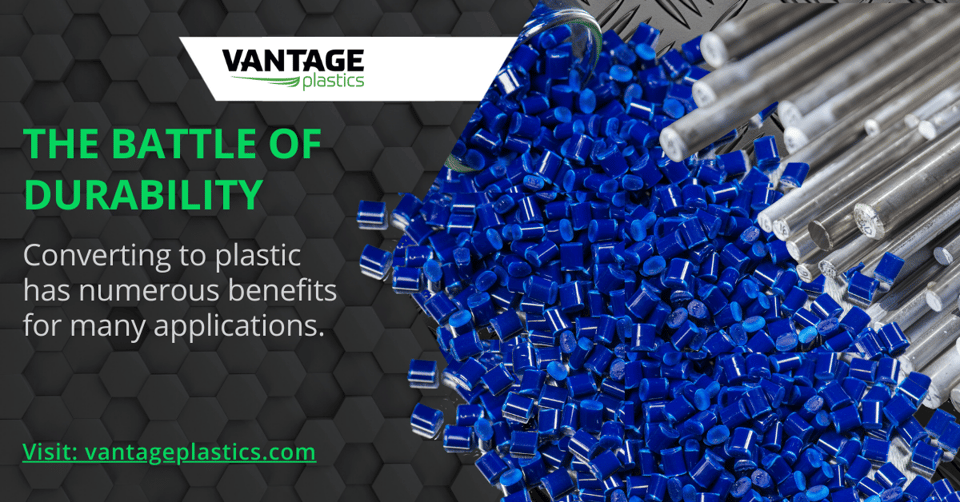
Thermoformed plastic is a versatile material used in various applications, including plastic pallets, packaging, and even medical devices. Unlike injection molding, thermoforming allows for alternative design flexibility, performance, and often lower costs, making it an ideal choice for many industries requiring high levels of customization and precision in their products.
TYPES OF ENGINEERED RESINS FOR METAL REPLACEMENT
Several types of engineered resins are available for metal replacement in thermoformed plastic products. The frontier of the capabilities of plastics continues to evolve as new compounds with specialized properties are continually being discovered. Vantage Plastics has developed customized blends of plastics to provide custom solutions for numerous customers. A dedicated innovation team within Vantage Plastics continuously researches specialized blends of plastics, including the incorporation of renewable organic materials. Each resin has its unique set of properties and advantages that make it suitable for specific applications, including:
- Acrylonitrile Butadiene Styrene (ABS)
- High Density or High Molecular Weight Polyethylene (HDPE) or (HMWPE)
- High Impact Polystyrene (HIPS)
- Polycarbonate (PC), Polyetherimide- Ultem (PEI)
- Thermoplastic Polyolefin (TPO)
- Polypropylene (PP)
- Polymethyl Methacrylate-Plexiglass (Acrylic)
- Polyethylene Terephthalate Glycol (PETG)
BENEFITS OF REPLACING METAL PARTS WITH THERMOFORMED PLASTIC PARTS
Thermoformed plastic parts have been a game changer in the manufacturing and engineering industries, offering cost-effective and versatile solutions for various applications.
COST EFFICIENCY OF THERMOFORMED PLASTIC PARTS
Cost efficiency is one of the primary benefits of thermoforming plastic. Metals counterparts like stainless steel can be up to three times more expensive than plastic for producing identical parts, making thermoforming a more economical choice for manufacturing.
- Reduced material costs with thermoformed plastics: Utilizing plastic sheets instead of metals reduces raw material expenses and contributes to overall cost savings.
- Lower production expenses due to simpler processes: Unlike complex injection molding techniques, thermoforming requires fewer steps, reducing labor and production rates.
SHORTER LEAD TIMES AND PRODUCTION PROCESSES
The thermoforming process offers manufacturers shorter lead times than sheet metal fabrication, allowing for faster product delivery. Shorter lead times and production processes can result in faster turnaround time for product manufacturing and a more streamlined workflow.
- Faster turnaround time for product manufacturing: Thermoformed plastic parts can be produced more quickly than their injection molding or sheet metal counterparts, ensuring timely delivery of products.
- Streamlined workflow with less complex procedures: The efficiency of thermoforming allows manufacturers to meet tight deadlines without compromising on quality or performance, ensuring customer satisfaction and repeat business.
GREATER DESIGN FLEXIBILITY
As part design complexity increases, metal part costs rise exponentially due to additional steps required for intricate designs. In contrast, thermoformed plastics offer greater design flexibility without drastically increasing production costs or compromising quality. Some key benefits include:
- Enhanced customization options with thermoforming: Thermoformed plastic parts provide various design possibilities, enabling engineers and designers to create complex shapes and structures that may be difficult or costly with traditional metals.
- No exponential cost increase for intricate designs: Unlike sheet metal fabrication, thermoforming does not require additional labor-intensive processes such as welding or bending, resulting in consistent pricing even as design intricacy increases.
ENHANCED DURABILITY AND PERFORMANCE
Contrary to common misconceptions about plastic being fragile or weak, modern-day thermoplastics are highly durable materials suitable for various applications. Thermoformed plastics provide comparable strength to sheet metals but at a fraction of the weight – lighter products without sacrificing performance capabilities.
- Weight reduction benefits: By using thermoformed plastics instead of sheet metal, manufacturers can create lightweight products without compromising their structural integrity or functionality.
- Improved resistance against wear and tear over time: Thermoformed plastic components can withstand harsh environments and maintain their functionality for extended periods, unlike metal parts that may corrode or deteriorate.
- Better performance in harsh environments: The chemical properties of thermoformed plastics make them more resilient to extreme temperatures, moisture, and other environmental factors that could negatively impact the performance of metal components.
ENVIRONMENTAL BENEFITS OF USING THERMOFORMED PLASTIC PARTS
The use of thermoformed plastics contributes positively towards sustainability efforts by minimizing waste generation during production processes. Modern advancements have led to the development of eco-friendly materials that help reduce environmental impacts further.
- Reduced waste through precise molding techniques: Thermoforming allows for accurate and efficient shaping, resulting in less material wastage compared to traditional manufacturing methods.
- Environmentally friendly options: Innovations such as biodegradable and recyclable plastics offer a more sustainable alternative for manufacturers looking to minimize their ecological footprint.
VANTAGE PLASTICS IS YOUR THERMOFORMED PLASTIC PARTS EXPERT
Utilizing thermoformed plastic can greatly benefit manufacturers and engineers seeking a reliable solution for their projects while also reducing costs and environmental impact. If you are utilizing materials other than plastics, consider a conversion. Converting to plastic may very well provide an improved outcome on several fronts. Contact us today to learn more about how Vantage Plastics can help you achieve your project goals with our thermoforming capabilities.