The Thermoforming Process Explained
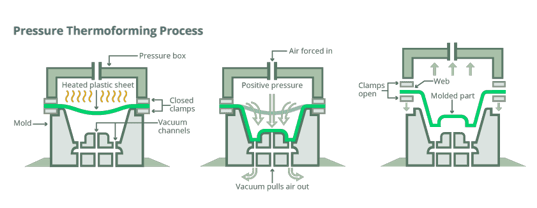
On the surface, thermoforming is pretty basic. A sheet of plastic is heated and made pliable, then stretched over a mold so the plastic takes on the mold’s shape to create whatever part is needed, be it a 6-door panel, a pallet, a swimming pool, or any of hundreds of other products.
Thermoforming has many advantages over other plastic production processes. Thermoforming is faster, less expensive, and more versatile. With thermoforming, you can create larger parts more easily. For example, at Vantage, we can produce products with a draw as deep as four feet (4’) and as large as nine-and-a-half feet by seventeen-and-a-half feet (9’ 6” x 17’ 6”) and anything in between.
In this article, we explain the Vantage Plastics 6-step thermoforming process from start to finish. We are vertically integrated and can turn a concept into a finished product all in-house. This allows us to truly be a “One Stop Shop” for customers.
THE VANTAGE THERMOFORMING PROCESS
There are two core activities in thermoforming: heat and forming. But ensuring that those activities are achieved to perfection requires supporting actions. Here are the phases a product goes through from when it enters our door as a concept to the time it leaves as a finished product. Each step plays a crucial role within a product’s thermoforming development.
STEP 01: ENGINEERING (INTAKE, QUOTING, DESIGN)
When a client brings us a project or concept, it first goes to our application engineers. They work with customers to clearly understand the nature of the project, the goals, and how we can create a solution. The application engineers gather all necessary information for the project and disseminate it to the team. The engineers also stay with a project throughout its life in our facility, communicating with the customer throughout the process.
After the application engineers have gathered all the info and have an understanding of the project, they turn it over using a Design Specification Form (DSF) to our sales engineers. The sales engineers create a design concept that is used to develop a pricing quote for the project. The quote includes pricing for the following services:
- formal design
- prototype tooling with formed samples to view, test, and tweak if needed
- aluminum production tool
- production samples to view and test
- production
After the client accepts the quote and places an order, the project is passed along to our project engineers. This team creates 3D models and FEA analysis of the desired part. This provides a clear visualization of the finished product, which is helpful for identifying shortcomings or needed correction and avoiding costly mishaps down the line.
After the client approves and the project engineers confirm a design, the project is ready for the next step of the process.
STEP 02: TOOLING
The first step of the tooling phase is the creation of a prototype tool. Working with our exclusive partner, Contour Engineering, we create a wooden prototype mold. It serves as a rough draft of the final product and is used to test product designs before production. The wooden prototype is used to create samples of the finished product for the customer to inspect and review. Wooden prototypes are extremely beneficial. They ensure the product is accurate. They also allow the customer to make last-minute changes before the parts go into production. Once it is approved and the customer is happy, the prototype is used to create an aluminum production tool. Product samples are created from the aluminum tool. The samples are reviewed by the customer. Once the samples are approved, the product goes into production.
STEP 03: MATERIAL SELECTION
Once the aluminum tool is approved for production, our sister company, Edge Materials Management, may get involved to help choose the right material. Edge is an on-site plastics recycling facility. They grind trays, pallets, plastic scrap, along with other appropriate plastics. Their output allows us to offer our customers the option of using regrind material for production, which can reduce cost while also benefiting the environment.
Once a material is chosen, we enlist the expertise of Airpak Plastics. Airpak can extrude sheets of plastic in widths up to 88” wide and thicknesses from 0.030” to 0.450.” They can also run A-B-A sheets that put a different color on each side of the sheet. They can also create laminated prints on sheets. All of this is done in-house, within our own facility.
STEP 04: PRODUCT VERIFICATION; FULL PRODUCTION
Once the product is made, it undergoes performance testing. In this phase, we test for strength and functionality. This stage verifies that all customer requests have been satisfied and the product is ready for a full run of production. We go through every step necessary to ensure our products are exceeding our customer requirements.
STEP 05: PRODUCTION
With a production mold in hand and production samples approved, production begins. We run the part through the thermoforming process, in which the sheet of plastic is heated, stretched over the mold, and pulled into the cavity of the mold using vacuum pressure. Within our facility, we have eight single-sheet machines and five twin-sheet machines. Depending on the size of the job and the quantity of parts, production can take days or weeks.
STEP 06: SHIPPING LOGISTICS
After production, our dedicated shipping department can work with you to arrange shipping to your desired locations both within the United States or internationally using various forms of transportation.
CHOOSE THE CUSTOM THERMOFORMING MANUFACTURER YOU CAN TRUST
At Vantage Plastics, we design and manufacture many types of thermoformed products. All of the steps of our process are performed in-house, ensuring customers get undivided attention. Within our facility, we have six single-sheet machines, five twin-sheet machines, and one sample machine dedicated to prototype samples. Anything needed for shipping or storage, we can create a package for it.
We have many solutions to meet your unique requirements. Contact us or call 989-846-1029 to discover how we can serve you!