Vantage Plastics has decided to step in to help with the shortage of Personal Protective Equipment...
How Does Prototyping Ensure Better Products?
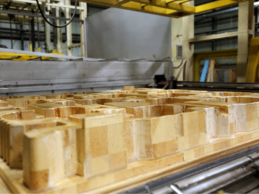
In the world of thermoforming, prototyping is the front-end process in which a temporary tool (mold) is developed to test parts for fit, function, and performance.
Prototype tools can be made out of wood, REN board, or 3D printed. In all cases, these prototype tools are inexpensive to make compared to aluminum production tools. They also provide rapid turnaround time.
Prototypes are used to make sample parts that can be reviewed for fit and function and if they need to be changed. Making changes to prototype molds is much easier and cheaper than production molds.
In this article, we look at different aspects of prototyping and what makes Vantage Plastics a leader in prototype thermoforming.
MATERIALS USED FOR THERMOFORM PROTOTYPING
Three materials are primarily used for thermoforming prototypes:
- Wood
- RenShape Board
- 3D-Printed Plastics
WOOD
With wood, the material must be clear and without knots to prevent any kind of defects in the part that’s produced.
The limitation with wood is that during the sampling process where they’re forming the plastic over the tool, you can only get a few test parts — maybe 10 or so – before the wood starts to deteriorate. Because the wooden molds are eventually used to make the dies for the aluminum molds, the challenge here is to keep the damage of the wood mold to a minimum.
RENSHAPE BOARD
RenShape board is a medium-density polyurethane modeling and styling board. It is an ideal material for models and prototypes, master patterns, and tooling aids. It produces very stable, dimensionally accurate parts with well-defined edges and surface detail. RenShape board holds up longer and lets you make more parts during the sampling process.
3D PRINTING
3D-printed prototypes are a new player to the field. 3D molds can be made from a variety of materials, are highly refined, and hold up longer. With the right material, you can even make short-run production parts from 3D prototype molds. Of the three prototype materials described here, 3D-printed prototypes are the most expensive.
WHO USES THERMOFORM PROTOTYPING?
Most industries and manufacturers use prototyping to some degree. The advantage is, once you have a prototype and you make samples from it, it opens the door to tweaking the final part. You can check for fit and function, you can do compression tests, and more. For example, for racks and trays, you can make sure the trays don’t crush the parts inside.
You can do vibration testing to see whether the container is protecting the parts that they’re shipping across highways across the country. Trucks are going to rattle. With prototype racks, you can test to see if the parts are captured well enough in the tray to stay secure.
Similarly, in the recreational markets for things like sleds or kayaks, a prototype lets you determine if you like a feature before you commit to making thousands of them. That’s one of the big advantages of prototyping — you can modify a product before it goes into production tooling.
REAL-WORLD EXAMPLES
In the automotive industry, companies change part designs at the prototype stage. That means the storage containers for those parts must also change to accommodate the altered part.
Electric vehicle battery packaging is an example. As we get containers ready for batteries, manufacturers are changing the battery configuration. Perhaps they add a hose someplace or an outlet someplace. That might involve changing the shipping and storage containers. But that’s the last thing that the battery engineers think about when designing the parts. So having prototype containers rather than production containers means we can accommodate the changes before going to production.
WHY CHOOSE VANTAGE PLASTICS FOR PROTOTYPE THERMOFORMING?
Why choose Vantage Plastics for thermoforming? Four primary reasons.
- Vantage Plastics, unlike most thermoformers has a dedicated prototyping operation. We have a sister company, Contour Engineering, that is dedicated to us. We have an exclusive relationship with Contour services. Many other thermoformers go to an outside prototype toolmaker. Not us.
- We have a dedicated tool department with very skilled tradespeople who have long tenure in the industry. We can quickly make modifications in-house.
- Reason number three to choose Vantage is we are continually adding more machines and more talent to give us greater flexibility.
- Vantage has a highly skilled and experienced design and engineering group that are able to create tool models for a wide variety of projects and market applications.
CONTOUR ENGINEERING SPECIALIZES IN PROTOTYPE THERMOFORMING
Contour Engineering is a custom tool and die shop that transforms ideas into reality. Their focus is prototyping, tooling, molding, and dunnage operations. Contour develops custom tooling solutions for a variety of clients. Many of their clients are dunnage and packaging specialists, thermoformers, RIM, and other mid-sized manufacturers.
Contour Engineering services include:
- DESIGN SERVICES. They take your ideas, drawings, and CAD files and transform them into high-quality tooling.
- TOOLING DEVELOPMENT. They develop tooling to produce components and products with high accuracy.
- PROTOTYPING. They create a plan and do a test run to see if the product meets our quality standards or could be improved.
- CUSTOM SERVICES. They make prototypes and produce tooling to your exact specifications.
THERMOFORM PROTOTYPING FROM PLASTICS DELIVERS REAL BENEFITS
Discover how thermoform prototyping from Vantage Plastics can help you. Contact a Vantage Plastics prototyping expert today.