Plastic thermoforming is a versatile manufacturing process that has revolutionized the production...
Plastics Used in Thermoforming
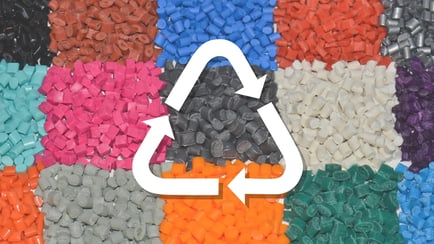
Thermoforming is one of the most versatile plastic part-making processes on the planet. Parts of the versatility come from the fact there are many different plastics that can be used in thermoforming.
A WIDE RANGE OF PLASTIC CHOICES FOR THERMOFORMING
A range of plastics can be used in Thermoforming. Some commonly used plastics include:
- Acrylonitrile Butadiene Styrene (ABS)
- High Density or High Molecular Weight Polyethylene (HDPE) or (HMWPE)
- High Impact Polystyrene (HIPS)
- PMMA/PVC blend (KYDEX)
- Polycarbonate (PC), Polyetherimide- Ultem (PEI)
- Thermoplastic Polyolefin (TPO)
- Polyvinyl Chloride (PVC)
- Polypropylene (PP)
- Polymethyl Methacrylate-Plexiglass (Acrylic)
- Polyethylene Terephthalate Glycol (PETG)
Depending on the application, several factors are considered when choosing the appropriate material(s) to use.
These factors can include:
- material stiffness
- hardness
- impact strength
- heat deflection
- tensile strength
- forming properties.
Other considerations when choosing materials may include selecting additives to address issues such as chaffing, electrostatic dissipation, rust inhibition, coloring, and coefficient of friction, among others.
HMWPE OR HDPE IS THE PLASTIC OF CHOICE FOR THERMOFORMING
While Vantage Plastics can work with all of the indicated materials, its primary material is High Molecular Weight Polyethylene or High-Density Polyethylene (HMWPE or HDPE). This is a very robust material that is resistant to cold temperatures, can sustain high impact without damage, is resistant to chemical interaction, and is a great choice for smart packaging/material handling and many other applications.
While dimensional stability can vary with ambient temperature, industry standards allow for achieving fairly tight product tolerances. This material can also be blended with additives to achieve solutions for various unique applications.
FIVE THERMOFORMING PLASTIC EXTRUSION LINES
Vantage Plastics currently has five extrusion lines within its subsidiary called AirPark Plastics to produce the sheet used by its thermoforming machines. These extrusion lines extrude an average of around 120,000 pounds of resin per day. This is the equivalent of eight to ten railcars per month. During the course of a year Vantage Plastics extrudes approximately forty-eight million (48,000,000) to fifty million (50,000,000) pounds of resin through AirPark Plastics. This extruded sheet is then used to form products.
Relative to the resin that is extruded by AirPark Plastics approximately fifty percent (50%) is recycled material. “Forming Sustainable Futures” is one element of the three-pronged mission of Vantage Plastics. Since Vantage Plastics strongly believes in this element it is very active in recycling initiatives within the state of Michigan and elsewhere. As a result Vantage Plastics formed another subsidiary called Edge Material Management. This subsidiary seeks post industrial plastics and backs up the Vantage Plastics guarantee to buy back any product Vantage makes for its material value after it is no longer needed by a customer. Edge Material Management has the ability to reclaim plastics by grinding and re-pelletizing the plastic so it can be re-extruded and used to make new products.
DISRUPTIONS IN PLASTIC RESIN SUPPLY CHAINS
While there have been disruptions in the plastic resins supply chain during the last couple years causing volatility in pricing and availability, Vantage Plastics has strong relationships with multiple plastics streams to help control these risks. In many cases price adjustment formulas are built into longer term purchase orders to account for resin price fluctuations. These are generally tied to an independent third-party index.
When it comes to specialized materials and plastic blends, Vantage Plastics is conveniently located in Northeastern Central Michigan near other businesses that specialize in material compounding. Over the years, Vantage Plastics has developed strong relationships with compounding specialists to develop proprietary compounds to achieve unique customer-driven solutions. “Forming Solutions” is another element of the three-pronged mission of Vantage Plastics. A dedicated innovation team at Vantage Plastics supports research and development that provides unique solutions to the customers of Vantage Plastics that are unavailable anywhere else on the planet.
LET VANTAGE HELP YOU WITH PLASTIC RESIN SELECTION FOR THERMOFORMING
Contact Vantage Plastics and let our team of experts help determine a solution that best fits your needs. Our Application Engineers have many years of experience and can help you identify opportunities where our capabilities can yield improved results.