Twin-sheet thermoforming offers a multitude of functional benefits that significantly enhance...
Twin Sheet Thermoforming
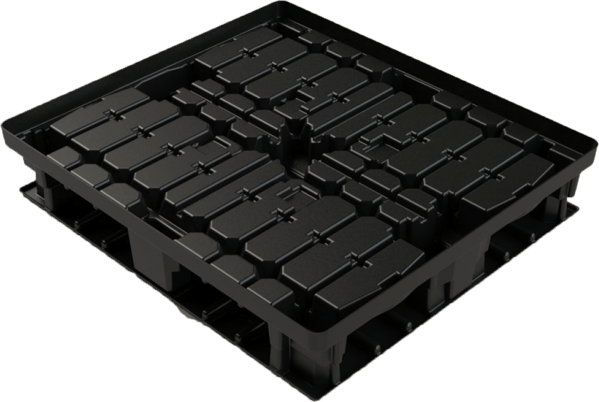
In this article, we define twin sheet thermoforming and describe its unique uses.
HOW TWIN SHEET THERMOFORMING WORKS
In traditional thermoforming, a single sheet of plastic is heated and then shaped over a mold to form the finished product.
In twin sheet thermoforming, as the name implies, two sheets of plastic are used. Each sheet is placed over an opposing mold, heated, and then perfectly aligned at their edges and then compressed while still hot to form a single product. This compression process essentially welds the two pieces together at touch points across the structure. In some cases the finished product can be designed with a cavity that can be left empty. This is useful, for example, if the product being made is a container or ductwork, or it needs to be filled with other mechanical elements or electrical wires or material such as foam or insulation. In many cases where very heavy loads of material are being transported in plastic dunnage containers or pallets, steel, aluminum, or carbon fiber bars can be inserted between the two sheets to create extremely strong plastic product performance.
BENEFITS OF TWIN SHEET THERMOFORMING
Twin sheet thermoforming offers the advantage of creating a hollow part without having to use adhesives or fasteners.
Another advantage is that twin sheet products are less costly to manufacturers that blow molded or rotational molded parts, but twin sheet parts can be made to be much more cosmetic.
Other advantages of twin sheet thermoforming are:
- Lower tooling cost
- Variable material thicknesses and colors
- Improved structural rigidity
- Ability to form hollow parts into which other components, such as metal or carbon fiber bars, electrical wires or conduit, can be inserted
- Can include internal reinforcements such as foam for insulation or sound deadening
- Molded attachments are available
- Can accommodate multiple textures and have variable wall sizes
- Inner and outer surfaces can have differing finishes
- Available in multiple materials and sizes
PARTS MADE FROM TWIN SHEET THERMOFORMING
A wide variety of parts can be made from twin sheet thermoforming. It is suitable for parts that require maximum durability, a secure structure, weight bearing capacity, and is as lightweight as possible.
Twin sheet thermoforming is ideal for parts, panels, and enclosures that will be seen from both sides, that need strength, or that will house mechanical parts, electrical parts, or insulation.
Examples of twin sheet products include:
- Large doors
- Component panels
- Vending Machines
- Bed Liners
- Air Ducts
- Shrouds & base covers
- Equipment enclosures
- Pallets
- Cases and Containers
PROBLEMS TO AVOID DURING TWIN SHEET THERMOFORMING
Because it involves two sheets, twin sheet thermoforming has its own set of unique challenges. These include:
THE NEED FOR PRECISE MOLD ALIGNMENT
Twin sheet thermoforming traps a pocket of heated air between the sheets. During cooling, that pocket could collapse. To prevent this, vent holes are designed into the molds. These allow cool air to get inside the panel, helping prevent collapse and controlling the cooling process. Care must be taken to ensure the holes are properly sized to provide enough cooling, but without compromising the finished appearance of the product.
DRAW RATIO LIMITS
In single sheet thermoforming, parts can be designed with 3:1 draw ratios and deep undercuts. Plug assist makes this possible. In plug assist, extra material is pushed into the mold to reduce wall thinning at corners and cuts. But plug assist is not an option in twin sheet forming because additional material cannot be injected into the cavity. For this reason, twin sheet panels must have wider radii at corners, along the smaller draw ratios.
SHADOWING
In twin sheet thermoforming, shadowing is the visible variation in a surface finish. It often occurs at spots adjacent to where the sheets are pressed together. If a panel is going to be painted, or the shadowing occurs in a non-appearance area, shadowing is not an issue. Otherwise, it is. Ways to fix or prevent shadowing include bead blasting the mold so that the entire finished panel has a textured finish. This hides the shadowing.
Another solution is to hide press points as much as possible (for example, beneath an attachment) so shadowing is not visible. Either way, shadowing must be taken into consideration when designing twin sheet parts.
SHEET THICKNESS
In twin sheet thermoforming, one of the sheets usually bears the brunt of the load bearing for the product. This sheet is usually thicker than the other one. In such cases, it is best to keep the difference in thickness between the two sheets to 0.0625 in. or less. Larger thickness put the twin sheet product forming out of sync, which could lead to warpage during heating and cooling cycles.
TWIN SHEET THERMOFORMING PLASTICS AND SPECIFICATIONS
The following plastics can be used for twin sheet thermoforming.
- TPO – Thermoplastic Polyolefins have high impact resistance and can keep up performance in cold and high heat applications
- ABS – Acrylonitrile Butadiene Styrene can be used across a number of products due to its impact and chemical resistant properties
- HDPE – High-Density Polyethylene Sheets have a high impact strength and are used for industrial products
- HIPS – High Impact Polystyrene is lightweight, inexpensive, and is commonly used in food packaging and housing applications
- Acrylic – Acrylic carries great shatter resistance, weather resistance, resilience, and pliancy
FORMING TOLERANCES
At Vantage Plastics, our thermoforming equipment is calibrated to the following specifications.
- 0 – 12”: +/- .006”/inch
- 12” – 65”: +/- .005”/inch
- 65” and over: +/- -.004”/inch
- Holes: +/- .015” up to 1”
Notes:
- When using HDPE it expands and contracts at a rate of 0.00010” x length of plastic per degree of temperature change.
- Example: 0.00010 x 96.00 x 100 (degree of change) = 0.96”
- Unless otherwise specified, tolerance data is based on information from “The Society of the Plastics Industry Inc.” revised 1991 standards practices of plastics molders (HDPE). Also based on manufacturing temperatures ranging from 70-90 degrees Fahrenheit.
VANTAGE PLASTICS — DOUBLY GOOD AT TWIN SHEET THERMOFORMING
Interested in exploring how twin sheet thermoforming can benefit you, especially compared to blow or rotational molding? Give us a call at 989- 846-1029 or contact us today.