The Advantages of Custom Heavy Gauge Thermoforming
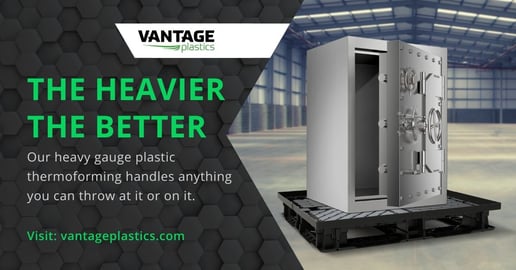
Heavy gauge thermoforming at its core involves heating thick plastic sheets until they become pliable. Once malleable, these sheets are shaped using vacuum or air pressure techniques to form to bring them in compliance with production tooling to develop functional and sturdy products. The process is favored for its ability to create rigid enclosures for sophisticated equipment and components.
TYPES OF HEAVY GAUGE THERMOFORMING
Heavy gauge thermoforming, using sheets up to .5” thick, offers versatile methods for creating durable products. Let’s explore these techniques:
- Vacuum Forming: Simple and widely used, a hot sheet is formed over a mold using vacuum pressure.
- Pressure Forming: Ideal for highly cosmetic parts with fine detail, pressure forming employs pressure and vacuum to draw the sheet tightly to the mold.
- Twin Sheet Forming: Two heated sheets are formed simultaneously, then pressed together with air to create extremely strong and rigid parts.
- Fabrication: The sheet is bent and bonded into the desired shape, offering endless design possibilities with minimal tooling costs.
HEAVY GAUGE THERMOFORMING APPLICATIONS
Heavy gauge thermoforming finds wide applications across diverse industries, encompassing a variety of product types. Here is a selection of common products made using heavy gauge thermoforming:
- Pallets
- Dunnage trays
- Totes & Bins
- Housings
- Enclosures
- Bezels
- Guards
- Radomes
- Components
- Recreational products
- Endless additional applications
MATERIALS USED IN HEAVY GAUGE THERMOFORMING
The choice of materials plays a crucial role in the performance and functionality of thermoformed products. Different plastics can be used depending on the specific requirements of the end product.
For example, heavy gauge polycarbonate is known for its exceptional durability and lightness, making it an ideal choice for protective screens or visors. Other materials like ABS, HDPE, and PETG also find application in various industries due to their specific properties, such as impact resistance, chemical resistance, and transparency. Vantage Plastics has the capability to develop unique material compounds based on customer solution requirements.
ADVANTAGES OF CUSTOM HEAVY GAUGE THERMOFORMING
Let’s dive into the numerous advantages of heavy gauge thermoforming, a transformative manufacturing process with a multitude of benefits.
COST-EFFICIENCY
One of the most significant advantages of heavy gauge thermoforming is its cost-effectiveness. The durability and longevity of thermoformed products enable them to withstand repeated use without compromising quality, leading to lower maintenance and replacement costs over time. Moreover, the relatively low tooling costs associated with the process make it an attractive option for both small and large-scale production runs.
Heavy gauge thermoforming offers reduced setup times and tooling expenses compared to other manufacturing methods like injection molding or die-casting. This cost-efficiency empowers businesses to allocate resources to further essential product development and innovation aspects.
FLEXIBILITY IN DESIGN AND AESTHETICS
Another compelling advantage lies in the design flexibility offered by heavy gauge thermoforming. Manufacturers can easily achieve intricate shapes, contours, and textures, making it possible to create highly customized and visually appealing products. This creative freedom is particularly beneficial when developing products with unique branding requirements or complex design specifications.
In addition to design versatility, heavy gauge thermoforming allows for integrating additional features directly into the forming process. This includes features like undercuts, inserts, and logos.
VERSATILITY ACROSS INDUSTRIES
Heavy gauge thermoforming has applications in various industries due to its versatility and ability to produce durable, high-quality products. Some of the industries that commonly use heavy gauge thermoforming include:
- Medical and Healthcare: Heavy gauge thermoforming is used to manufacture protective enclosures for critical medical devices like MRI machines, ultrasound scanners, and diagnostic equipment. These enclosures ensure the safety and functionality of sensitive medical instruments.
- Automotive: Heavy gauge thermoforming is used in the automotive industry to produce various components, including interior panels, instrument panels, dashboards, and protective covers. Thermoformed parts balance strength and lightweight design, making them ideal for automotive applications.
- Consumer Goods: In the consumer goods industry, heavy gauge thermoforming is employed to manufacture a wide range of products, such as packaging, containers, housings for appliances, and retail displays. The process allows for the cost-effective production of aesthetically appealing and durable products.
- Industrial and Machinery: Heavy gauge thermoforming is used to create custom components and enclosures for industrial machinery, ensuring durability and protection in harsh operating environments.
- Aerospace and Defense: In the aerospace and defense sectors, heavy gauge thermoforming produces various components, including aircraft interior panels, protective covers, and military equipment enclosures.
- Material Handling Products: Reusable, returnable, and recyclable across all industries
THERMOFORMING CONTRIBUTES TO A CIRCULAR ECONOMY
Most thermoplastic materials used in heavy gauge thermoforming are highly recyclable, significantly reducing landfill waste during the production process and product end of life. This eco-friendly characteristic aligns with sustainable manufacturing practices and environmental stewardship.
LOOKING FOR A HEAVY GAUGE THERMOFORMING SOLUTION?
The transformative power of custom heavy gauge thermoforming opens doors to innovation, enabling businesses to develop products that meet the highest performance and durability standards. By embracing this versatile manufacturing process, companies like Vantage Plastics offer solutions that cater to specific needs and deliver excellence at an affordable cost.
If you’re ready to unlock your products’ potential for innovation and durability, contact our experts at Vantage Plastics today.