Heavy Gauge Plastic Uses
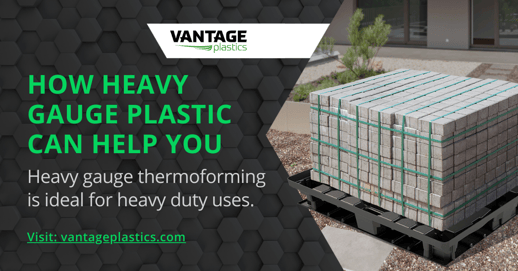
When you have plastic components made, you sometimes just want something light and simple. But sometimes your business has heavy-duty needs that require strength and the ability to withstand anything. That’s when it’s time to consider heavy gauge thermoforming. Let’s delve into what that process involves.
SO WHAT IS HEAVY GAUGE THERMOFORMING?
Heavy-gauge thermoforming means – you guessed it – using a thicker gauge plastic, usually up to half an inch thick. It’s the process of turning that sheet of plastic into a usable form with low pressure, complexity, and cost. The machinery involved is different than that used for lighter gauge. The plastic is usually sheetfed rather than inserted from a roll, for example.
HOW IS IT MADE?
There are a few different processes for heavy gauge thermoforming, such as:
- Vacuum forming: This involves forming a hot plastic sheet over a mold and pulling it tight by applying a vacuum.
- Pressure forming: Here the plastic sheet is pressed by the mold all while a vacuum is applied. Good for applications needing fine surface detail.
- Twin sheet forming: This is where two sheets of plastic are pressed into molds, then pressed together. When together, air is injected adding pressure.
- Fabrication: The most straightforward shaping process, fabrication involves bending the plastic into a new shape.
WHAT ARE THE ADVANTAGES OF HEAVY GAUGE THERMOFORMING?
Heavy-gauge thermoforming enables you to create large components that look good at a lower cost and minimum run than most other plastic manufacturing processes. The upfront tooling cost is also lower. An economically ideal run using heavy gauge processes would be around 10 to 500 pieces per year.
WHERE AND WHY IS HEAVY GAUGE THERMOFORMING NEEDED?
The heavier gauge means it’s frequently used for heavy-duty parts, things like:
- Pallets and dunnage: Shipping and storage involves heavy items getting bumped or dropped. Heavy gauge pallets or other containers help mitigate damage.
- Transportation interior cabin parts: These can include interior panels, seating, luggage racks among other things.
- Electronic enclosures: Having a heavier gauge shell helps protect delicate electronics.
- Exercise equipment: Gym equipment needs to withstand a lot of weight, force, and use, making a heavier gauge a good choice.
WHAT TYPES OF PLASTICS ARE USED FOR HEAVY GAUGE THERMOFORMING?
The choice of plastic used depends on what color or texture is desired, as well as any functional needs (ie: rigidity, degree of flame retardation, etc). Among the plastics used in this process are:
- Acrylic: used often for microprocessor housings.
- ABS: used in a number of different applications.
- HDPE: cost-effective while still having high impact strength.
- PVC: used often for microprocessor housings.
At Vantage, we’re well acquainted with a wide variety of plastics and can make recommendations based on your needs.
IT’S TIME TO GO HEAVY DUTY
Heavy-gauge plastic thermoforming might be just what your project needs. If so, you need to work with a partner equipped to make the heavy gauge products that will be a perfect fit. Contact Vantage Plastics today and talk with the experts to see what we can do for you.