Cost-Effective Thermoforming: Greener Shipping With Optimized Containers
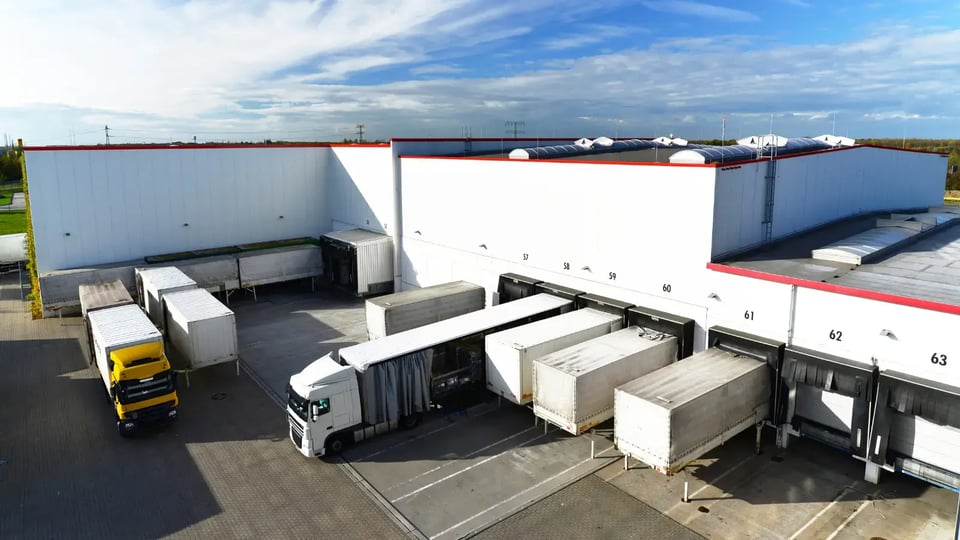
Shipping goods efficiently while minimizing environmental impact is no longer an abstract ideal; it is a practical, achievable objective through advanced logistical techniques. A critical challenge in modern logistics is maximizing container utilization while maintaining sustainable practices. Thermoforming emerges as a pivotal solution in this endeavor, revolutionizing eco-friendly shipping.
This process uses heat to mold plastic into custom, precise shapes that optimize container space, significantly reducing material waste and excess packaging. Thermoforming enables companies to boost container density and efficiency, lower shipping costs, and reduce fuel consumption by designing packaging that fits snugly around products. Implementing thermoforming in logistics offers businesses across industries—from retail to manufacturing—a scalable method to enhance sustainability while streamlining operations. Understanding and adopting this technology is key to creating more efficient, environmentally conscious supply chains.
Understanding Thermoforming in Shipping
In the fast-moving world of shipping, maximizing container usage and understanding life cycle analysis is critical. Doing so helps make shipping not only cost-effective but also environmentally friendly. One technique that plays a significant role here is thermoforming. This method can be a game-changer in creating efficient packaging solutions. Wondering how? Let’s break it down.
What is Thermoforming?
At its core, thermoforming involves shaping plastic sheets into proper customizable forms through heat. The primary methods involved are vacuum forming and pressure forming.
- Vacuum Forming: Vacuum forming is a simplified version of thermoforming, where a plastic sheet is heated to a pliable temperature and then stretched onto a mold. A vacuum is applied to suck the air out from between the sheet and the mold, pulling the plastic tightly against the mold surface. As the plastic cools, it retains the shape of the mold.
- Pressure Forming: Pressure forming is a more advanced thermoforming process than vacuum forming. In this method, heated plastic is placed over a mold, and instead of just using a vacuum to pull the plastic into shape, additional air pressure is applied from above. This higher pressure forces the plastic more firmly into the mold, resulting in greater detail and sharper features.
Applications of Thermoforming in Logistics
By maximizing space and minimizing waste, thermoforming supports both economic and environmental goals. Here's how:
- Custom Packaging Solutions: Thermoforming allows for precise, custom-shaped packaging that conforms to the product's dimensions. Using computer-aided design (CAD) modeling and vacuum forming techniques, thermoformed packages are designed precisely, reducing void space within shipping containers. This results in fewer trips needed for the same volume of goods, reducing fuel consumption and carbon emissions.
- High-Impact Protective Inserts: Injection molded inserts, designed with advanced polymer engineering, can be crafted to cushion sensitive items such as electronics, medical devices, and delicate industrial components. Using materials like high-density polyethylene (HDPE), polypropylene (PP), or thermoplastic polyurethane (TPU), these inserts provide shock absorption and rigidity, preventing product shifting or damage during transit. Engineers can incorporate features such as ribs, gussets, or contours to absorb impact forces, making them ideal for protecting fragile goods without the need for excessive secondary packaging. Vantage Plastics offers a proprietary material that can be used for inserts and provides a significant advantage over traditional insert materials. It is called VanTech.
- Optimized Trays and Pallets: Thermoformed trays and pallets offer significant advantages for large-scale shipping operations. Made from lightweight yet robust polymers like polycarbonate (PC) or thermoplastic polyolefin (TPO), acrylonitrile butadiene styrene (ABS), high-density polyethylene, high molecular weight polyethylene (HMWPE), these trays are designed to maximize container loading. Stacking configurations and nesting capabilities enable efficient storage and handling, reducing the need for manual labor and streamlining automated warehouse processes. Thermoformed pallets, often manufactured with reinforced ribbing or inserted structural bars, provide excellent load-bearing capacity while remaining significantly lighter than traditional wooden or metal pallets.
- Sustainability Through Recycled Materials: Many logistics applications are now embracing using recycled or recyclable thermoplastics. Thermoformed products such as dunnage, pallets, and trays can be made from post-consumer recycled (PCR) materials. If thermoformed products ever become damaged or are no longer needed, the materials they are made of can generally be recycled and made into entirely new products.
Maximizing Container Space With Thermoformed Solutions
Thermoformed solutions help maximize container density by providing unique, customizable options that ensure every inch counts.
Custom Thermoformed Inserts
Custom thermoformed designs provide a highly engineered packaging solution tailored specifically to product shape, weight, and fragility. Custom designs are manufactured through precise thermoforming processes to ensure a snug, form-fitting solution that minimizes wasted space, optimizes packing efficiency, and provides superior protection.
Consider the following benefits:
- Protection: Custom thermoformed packaging and when applicable, injection molded inserts are manufactured from high-performance materials, which offer exceptional durability and flexibility. These materials can be engineered to provide impact resistance, shock absorption, and rigidity. The snug fit eliminates product movement within the packaging, reducing the risk of surface damage, abrasion, or breakage during transport.
- Space Efficiency: Custom-fit designs ensure that every millimeter of the shipping container is utilized effectively. By minimizing voids and empty spaces within the packaging, companies can reduce the overall volume of shipments, allowing for more products to be packed per container.
- Versatility: The manufacturing process allows for intricate designs and contours to be formed, making them ideal for delicate items such as medical devices, electronics, and precision instruments, as well as more robust items like automotive components or industrial tools.
Stackable Thermoformed Containers
Stackable thermoformed containers are engineered to maximize vertical space in shipping and storage environments, offering a reliable and efficient solution for organizing and stabilizing loads. These containers, manufactured using precision thermoforming techniques, are designed with uniformity and strength, making them ideal for high-density stacking in manual and automated logistics operations.
Here's why they make a difference:
- Enhanced Loading Efficiency: Stackable thermoformed containers are designed with interlocking features that allow them to securely nest when stacked. This precise alignment enables quick and efficient stacking, reducing handling time and labor costs during loading and unloading processes.
- Better Space Utilization: One of the primary advantages of stackable containers is their ability to maximize available space, both vertically and horizontally. By leveraging the vertical space in warehouses, trucks, or shipping containers, companies can significantly increase the volume of goods transported per trip.
- Stability: Stackable thermoformed containers are engineered for structural integrity, ensuring loads remain stable even when stacked several layers high. Thermoformed containers can be designed with reinforced sidewalls or integrated stacking features, such as corner locking mechanisms, for additional load stabilization.
Cost Benefits of Thermoforming for Sustainable Shipping
Thermoforming, a highly efficient plastic molding process, has effectively optimized shipping operations by creating custom packaging solutions that maximize space and minimize waste.
Reduction in Shipping Costs
Optimizing container space with thermoformed solutions can cut down on your shipping costs. How? It's all about making the most out of every inch. Packing goods more efficiently results in:
- Increased Capacity: Custom thermoformed trays, inserts, and pallets optimize container loading, enabling a higher product density per shipment.
- Lower Fuel Costs: Fewer shipments mean reduced fuel consumption and lower transportation costs. Thermoformed packaging also tends to be lightweight, further contributing to reduced fuel usage.
- Decreased Handling Fees: With fewer shipments comes a reduction in handling costs, such as loading, unloading, and storage fees. The uniform design of thermoformed containers, trays, and inserts also facilitates easier stacking and automated handling, which can minimize labor expenses and reduce loading/unloading time in warehouses and shipping facilities.
- Thermoformed Products Are Robust: Therefore, reusable in many cases for years while retaining their integrity and functionality.
- At the End of Life, the Materials Retain Value: As they can be recycled and made into new products. Vantage Plastics has a guaranteed buy-back program for the materials in the products we manufacture.
Minimizing Material Waste
Thermoforming excels in reducing material waste while delivering precision-engineered packaging and products. This means:
- Reduced Raw Material Use: Thermoforming uses the minimum amount of plastic necessary for structural integrity. Thin-gauge thermoforming enables the use of thinner plastic sheets (less than 0.06 inches in thickness), which provides sufficient durability while dramatically reducing material use.
- Less Packaging Waste: By eliminating unnecessary layers of packing material, such as fillers, foam, or extra cardboard, thermoformed solutions streamline the packaging process and reduce the amount of material that would otherwise end up in landfills.
- Sustainable Practices: Excess material generated during the thermoforming process, such as edge trims or cut-offs, is collected, reprocessed, and recycled into new plastic sheets.
Environmental Impact of Efficient Container Usage
In the pursuit of greener logistics and reduced environmental impact, efficient container usage plays a crucial role in minimizing waste, lowering emissions, and optimizing resource utilization. By maximizing container space and incorporating sustainable packaging solutions like thermoforming, companies can significantly reduce their carbon footprint while improving operational efficiency. Let’s explore the technical aspects of how these changes contribute to a more sustainable future.
Lower Carbon Footprint
Shipping is one of the largest contributors to global greenhouse gas (GHG) emissions, with cargo ships and tractor trailers burning vast amounts of fuel and emitting significant amounts of CO2, nitrogen oxides (NOx), and sulfur oxides (SOx). However, efficient container usage offers an immediate and impactful way to reduce these emissions.
By optimizing container loading, companies can reduce the number of trips required to transport the same quantity of goods. Simply by shipping the same volume of freight using fewer containers and fewer trucks can result in a massive reduction in carbon emissions.
Sustainable Material Options
While optimizing container usage reduces the carbon footprint of transportation, the materials used in packaging also play a significant role in the environmental impact of shipping.
Thermoforming supports the use of sustainable materials, including recyclable plastics like PET, HDPE, and biodegradable polymers. These materials offer a significant advantage over traditional single-use packaging, as they can be recycled or naturally decompose without contributing to long-term environmental damage. Thermoformed packaging solutions made from post-consumer recycled (PCR) materials further reduce the demand for virgin plastic production, conserving natural resources and reducing energy consumption.
- Reduced Waste: Thermoformed packaging can be designed to minimize excess material, significantly reducing the waste that ends up in landfills. Additionally, the use of biodegradable materials ensures that any packaging waste that does occur decomposes naturally, reducing its environmental impact.
- Recyclability: Most thermoformed plastics are recyclable, meaning they can be reintroduced into the supply chain at the end of their lifecycle. This closed-loop system reduces the need for new raw materials and supports circular economy practices, aligning with global efforts to reduce plastic waste.
- Resource Conservation: Thermoforming uses less material compared to alternative packaging methods, reducing energy and raw material consumption during production. This conservation of resources results in lower emissions during the manufacturing process, further improving the sustainability of the entire supply chain.
Vantage Plastics’ Commitment to Sustainable Shipping Solutions
At the forefront of sustainable packaging innovation, Vantage Plastics is dedicated to offering eco-friendly thermoformed solutions that directly address the challenges highlighted in this article. By focusing on efficient material usage, custom-designed packaging, the integration of recyclable and biodegradable plastics, and efficient manufacturing processes, as well as a dedicated innovation team, Vantage Plastics helps companies optimize shipping processes while minimizing environmental impact.
Our expertise in thermoforming allows businesses to maximize container space, reduce transportation frequency, cut fuel consumption, and lower carbon emissions. With a commitment to sustainability, Vantage Plastics provides advanced packaging solutions tailored to each client’s needs, ensuring that your products are protected during transit while supporting greener business operations.
By leveraging Vantage Plastics’ innovative packaging technology, companies can not only reduce shipping costs but also take meaningful steps toward a more sustainable future, contributing to reduced waste, lower carbon footprints, and enhanced resource conservation in the logistics industry. Contact us today to get started.