Injection Molded Stacking Solutions in Automotive Manufacturing
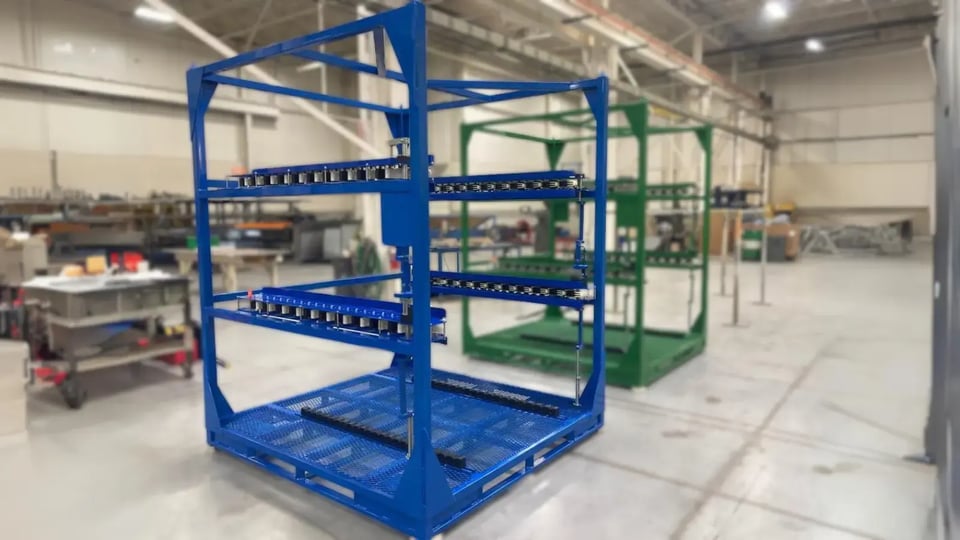
Stacking solutions protect Class A surfaces during shipping and handling. As car manufacturers strive to optimize production, these solutions offer a blend of efficiency and cost-effectiveness.
By minimizing waste and maximizing space, injection molded stacking solutions can seamlessly fit into high-demand production environments.
Injection Molding in Automotive Manufacturing
Injection molding has revolutionized automotive manufacturing, offering a powerful way to create durable and complex parts. With this technology, manufacturers can efficiently produce everything from tiny components to large panels with great precision.
Role of Stacking Solutions
Stacking columns improve how parts are stored, transported, and assembled by providing an organized and efficient system.
- Enhanced Storage: Stacking solutions optimize warehouse space by keeping components neatly arranged.
- Efficient Transportation: These solutions simplify the transport of parts between locations, reducing the risk of damage. It's like having cushioned seats for every ride.
- Streamlined Assembly: Stacked parts are easy to access on the assembly line, speeding up production.
- Automated Load/Unload: Fully automated systems enable seamless loading and unloading of parts, enhancing efficiency and reducing manual labor in high-volume manufacturing environments.
Key Applications in the Automotive Industry
Injection-molded stacking columns have become a cornerstone in handling various car parts. They offer many advantages—from reducing production costs to enhancing the durability of the components in logistic operations.
- Roof Panels and Hoods: Roof panels and hoods are vital to a vehicle's structure and appearance. Injection-molded stacking solutions streamline production and transportation, reducing costs.
- Doors and Sunroof Housings: Stacking columns provide precision handling for car doors and sunroof housings. By maintaining part separation and securing these components, the columns reduce the risk of warping or damage from environmental factors.
- Battery Casings: As electric vehicles become more common, the safe transport and storage of battery casings are critical. Stacking columns designed for battery casings help to secure these sensitive components, preventing damage and optimizing space. Their robust design helps protect the casings during transport, ensuring batteries remain safe from impacts and excessive heat.
- Seat Pallets: Weight and assembly efficiency are key in automotive seating. Stacking columns for seat pallets enable efficient storage and transport by allowing for precise stacking configurations. This reduces the overall footprint, making it easier to move and assemble pallets while maintaining part integrity.
Technical Aspects of Stacking Columns in Automotive Manufacturing
Stacking columns in automotive manufacturing can be fully automatic systems, significantly increasing storage capacity while maintaining precise part separation. These columns are versatile and are used in various applications, including shipping racks, WIP (Work In Progress) racks, line-side buffering, and LCA (Line-side Carton Access) systems.
Typical applications for stacking columns include:
- Shipping racks
- Tugger cart buffers
- Stationary buffer stations
- Accumulating buffer conveyors
- Seat pallets
Vertical Columns
Vertical columns represent the most common application in stacking systems. They feature customizable designs tailored to maximize the number of parts per pack. Providers can customize the finger and pitch (the distance between fingers) to fit specific parts, and the locking mechanism of the fingers allows for full part containment. This ensures that parts remain secure during transport and storage, reducing the risk of damage.
Key features of vertical columns include:
- Fully automated load/unload cells: These systems can operate autonomously, enhancing production efficiency.
- Material options: Fingers can be made from plastic, steel, or aluminum, depending on the application’s requirements.
- Applications: Ideal for shipping or WIP racks and buffering applications.
Additionally, injection molded brush dunnage within these systems provides additional part stabilization, especially when carts are in motion. The manual locking mechanism allows for securing any quantity of partially loaded racks, which is particularly useful in flexible manufacturing environments.
Vertical columns are also applicable in AGV (Automated Guided Vehicle) and cart applications, as well as pallet and shuttle conveyor systems, and they can feature latching styles that securely lock fingers in place.
Horizontal Columns
Horizontal columns are typically used in walk-in racks, where parts are supported by urethane dunnage and lean against spring-loaded fingers. The pitch in horizontal columns can be adjusted to accommodate almost any part, offering significant versatility in manufacturing processes. The locking mechanism ensures full part containment, and these systems can be integrated into fully automated load/unload cells.
Key features of horizontal columns include:
- Material options: Similar to vertical columns, fingers can be made from plastic, steel, or aluminum.
- Applications: They are used in shipping or WIP racks and buffering stations.
Angular Columns
Angular columns offer a unique opportunity to improve packing density by staggering parts within the stack. Like vertical and horizontal columns, the pitch can be customized, and the finger-locking mechanism ensures full part containment. These columns are also suitable for fully automated load/unload cells, making them ideal for high-volume production environments.
Key features of angular columns include:
- Material options: Similar to vertical and horizontal columns, fingers can be made from plastic, steel, or aluminum.
- Applications: They are used in shipping or WIP racks and buffering stations.
Stacking Solutions at LOTIS Technologies
LOTIS Technologies, a Vantage Plastics Family of Companies member, is a leader in delivering advanced stacking solutions tailored for the automotive industry and beyond. They leverage over 20 years of experience to customize stacking columns (available in injection molded, steel, aluminum, or composite materials) to your specific requirements. LOTIS specializes in injection molding, offering a wide range of capabilities, including:
- 1000 Ton Natco, 148oz Shot
- 500 Ton HPM, 75oz Shot
- 500 Ton Cincinnati, 48oz Shot
- 300 Ton Lombard, 36oz Shot
- 500 Ton Van Dorn, 60oz Shot
- 700 Ton HPM, 80oz Shot
- 1100 Ton HPM, 160oz Shot
These machines enable LOTIS to produce high-quality components like stacking columns, seat pallets, and custom dunnage with precision and efficiency. Additional services include expertise in design and prototyping.
At LOTIS, they focus on solving your packaging and manufacturing challenges with innovative, durable, and efficient solutions. Put their experience to the test and discover how they can contribute to your project’s success.