Lean manufacturing, a practice focused on minimizing waste while maximizing productivity, offers...
The Eight Wastes of Lean Manufacturing: And How to Eliminate Them
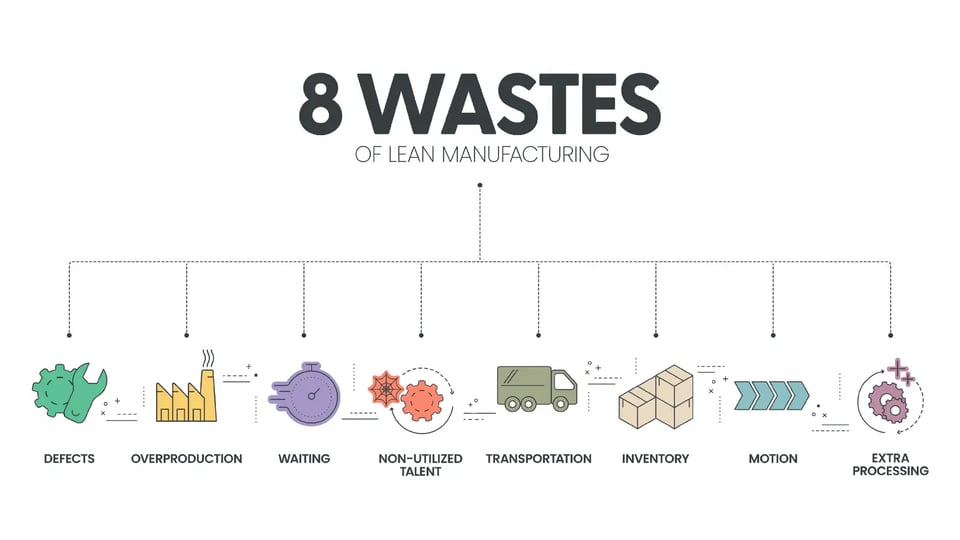
The impact of waste streams in manufacturing is significant, affecting not only the environment but also operational efficiency, costs, and regulatory compliance. By implementing lean principles, companies can leverage proactive solutions to minimize waste and maximize value creation, setting a new standard for operational excellence. Each waste stream, from defects to extra processing, presents an opportunity for improvement within the manufacturing landscape.
Operational excellence is at the core of every manufacturer’s process. Lean manufacturing principles help us identify and eliminate waste, improving productivity, reducing costs, and enhancing customer satisfaction. This article explores the eight wastes of lean manufacturing and provides insights into how we have successfully eliminated them.
Understanding Lean Manufacturing
Lean manufacturing is a methodology that aims to reduce waste while improving efficiency and quality in production processes. Let's delve into the origins and fundamental principles that define Lean Manufacturing.
The Origins of Lean Manufacturing
In 1910, Henry Ford and his associate Charles E. Sorensen created the first comprehensive manufacturing strategy. They arranged all the components of a manufacturing system—including people, machines, tooling, and products—into a continuous system to produce the Model T automobile. Ford's success was so great that he became one of the world's wealthiest men and revolutionized transportation. Many consider Ford the first proponent of lean manufacturing and just-in-time principles.Transportation Expenses and Storage
Key Principles of Lean Manufacturing
Value Identification: Lean manufacturing emphasizes identifying value from the customer's perspective. Understanding what the customer perceives as valuable helps streamline processes to deliver maximum value with minimum waste.
Waste Reduction: Central to lean manufacturing is the concept of eliminating waste in all forms - be it overproduction, excess inventory, waiting time, unnecessary transportation, over-processing, defects, or underutilized talent. By minimizing waste, resources are optimized, and productivity is enhanced.
Continuous Improvement: Continuous improvement, also known as Kaizen, is a core principle in lean manufacturing. It advocates for ongoing incremental process changes to gradually enhance efficiency and quality. This approach empowers employees at all levels to identify and address inefficiencies proactively.
Respect for People: Lean manufacturing also recognizes the importance of respecting and empowering employees. Organizations can create a culture of collaboration and innovation by valuing their insights, encouraging participation, and providing opportunities for growth.
The Eight Wastes of Lean Manufacturing
Let’s examine the eight wastes of lean manufacturing and the different strategies companies use to combat them.
1. Defects Waste
Defect waste represents the costs incurred from producing defective products that do not meet quality standards. These defects result in rework, scrap, customer returns, and even damage to brand reputation.
Common examples of defect waste include rework due to incorrect specifications, defective components, and faulty assembly processes. Companies can prevent defects at the source by implementing stringent quality control measures, conducting root-cause analyses of defects, and training employees on error-proofing techniques.
2. Overproduction Waste
Overproduction, a pervasive waste in manufacturing, occurs when goods are produced in excess of demand or before they are needed. Overproduction creates a domino effect in the waste stream, leading to excess inventory, increased lead times, and reduced flexibility in responding to customer needs.
Circumstances such as unclear customer needs, unstable production schedules, or delayed setup times can lead to a surplus in materials. Companies can identify and eliminate sources of overproduction waste by adopting a pull-based production system, setting up production leveling techniques like Heijunka, and closely monitoring demand signals.
3. Waiting Waste
This type of waste occurs when people or parts wait for the next production step. It is often caused by unbalanced workloads or inefficient process flows. Waiting waste occurs when materials, workers, or equipment are idle due to bottlenecks or delays in the production flow.
Examples of waiting waste include machine downtime, material shortages, and inefficient handoffs between workstations. Companies can reduce waiting times and enhance overall throughput by analyzing production schedules, optimizing machine setups, and implementing lean scheduling practices.
4. Talent Waste
Often, employees can be a company’s greatest asset. Underutilization of talent waste arises when employees' skills, knowledge, and creativity are not fully leveraged within the organization. This waste not only demotivates staff but also hinders innovation and continuous improvement.
Talent waste can include unutilized skills, lack of cross-training, and insufficient recognition of employee contributions. To address talent underutilization, companies should foster a culture of empowerment, provide training and development opportunities, and involve employees in decision-making processes.
5. Transportation Waste
Transportation waste involves unnecessary movements of products or materials within a facility. This not only delays the production process but also increases the likelihood of damage and defects and can even trigger other waste streams, such as waiting or motion.
Excessive handling, poorly designed production systems, and inefficient routing are typical examples that lead to transportation waste. To minimize transportation waste, companies can optimize their layout for more efficient material flow, utilize just-in-time delivery systems, and implement automated transport solutions.
6. Inventory Waste
Holding excess inventory ties up capital, takes up valuable space, and increases handling costs. To avoid these issues, companies often employ various inventory management techniques. One such technique is the Just-In-Time (JIT) inventory system, where inventory is ordered and received only when it is needed for production or sale. This approach ensures that inventory levels are kept at a minimum, reducing the amount of capital tied up in inventory, minimizing storage and handling costs, and reducing the risk of product obsolescence or spoilage.
Excess inventory waste can include situations such as obsolete stock, overpurchasing, and lack of visibility into inventory levels. By optimizing inventory levels through demand forecasting, implementing lean inventory management techniques like just-in-time, and establishing robust supplier relationships, companies can reduce carrying costs and improve responsiveness to market fluctuations.
7. Motion Waste
Motion waste refers to any unnecessary movement by employees and equipment that does not add value to the product. Excessive motion can lead to time wastage and physical strain.
Common examples of motion waste include spending excessive time locating tools, regularly walking back and forth to utilize equipment, or spending time locating vital information. To combat motion waste, companies can redesign workstations for ergonomic efficiency, standardize work processes to minimize motion variability, and provide employee training on proper handling techniques.
8. Extra Processing Waste
Overprocessing occurs when more work is done on a product than the customer requires. This often stems from poorly designed processes or misunderstandings about customer requirements. Overprocessing waste results from using more effort, time, or resources than necessary to complete a task or produce a product.
Overprocessing waste can stem from a lack of communication, inaccurate data, and excessive paperwork in documentation processes. To reduce overprocessing, companies should streamline production steps, eliminate redundant quality checks, and invest in technology that improves process efficiency and decreases the likeliness of error.
Lean Manufacturing—The Key to Our Success at Vantage Plastics
Partnering with a plastics processor that implements lean manufacturing practices, like Vantage Plastics, can significantly benefit your results. At Vantage Plastics, eliminating these eight wastes through lean manufacturing principles and continuous improvement is more than just a practice—it’s a cornerstone of our business strategy. It allows us to produce high-quality plastic products efficiently and sustainably, passing on the benefits of cost savings and superior product quality to our customers.
Let's use lean principles to create a more efficient and quality-driven manufacturing landscape. Contact us today for your plastic processing needs.