Benefits of Lean Manufacturing: Reducing Costs and Enhancing Product Quality
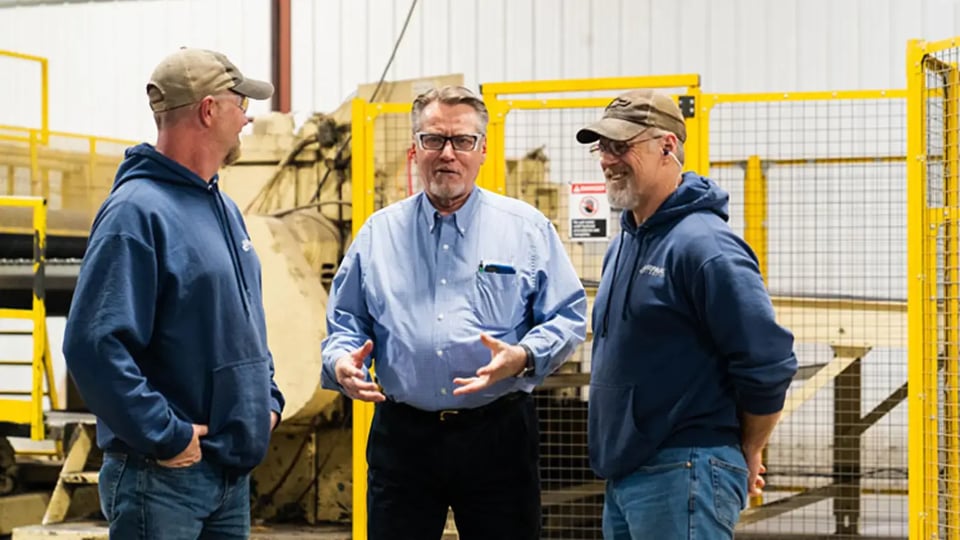
Lean manufacturing, a practice focused on minimizing waste while maximizing productivity, offers significant advantages to both manufacturers and customers. When combined with everyday manufacturing processes like thermoforming or injection molding, lean principles provide a powerful solution for manufacturers to improve the customer experience, reduce costs, and elevate product quality.
Companies like Vantage Plastics utilize lean manufacturing to deliver high-quality, cost-effective, and sustainable products, a win-win for companies and clients.
Understanding Lean Manufacturing
Lean manufacturing is a systematic approach that focuses on eliminating waste, optimizing processes, and enhancing overall efficiency in manufacturing operations. By leveraging fundamental lean manufacturing practices, companies aim to streamline production, reduce costs, and improve product quality seamlessly.
The Eight Wastes of Lean Manufacturing
Numerous challenges can impact manufacturing costs and product quality. These challenges not only increase production costs but also compromise the overall quality of the manufactured goods. The eight wastes of lean manufacturing include:
-
Transportation: Unnecessary transportation of materials or products between processes adds no value and increases the risk of damage, delays, and costs.
-
Inventory: Excess inventory ties up capital, occupies space, and can lead to increased handling and storage costs. It also risks material obsolescence and deterioration.
-
Motion: Unnecessary movements by workers or machines that do not add value can lead to wasted time and increase the risk of injury.
-
Waiting: Idle time occurs when processes are not synchronized, leading to delays and reduced productivity.
-
Overproduction: Producing more than is needed or before it is required results in excess inventory and increases costs.
-
Extra Processing: When process capabilities exceed product specifications, more work or higher-grade materials can be performed than necessary.
-
Defects: Production of defective items necessitates rework or scrapping, which adds significant costs and wastes resources.
-
Non-Utilized Talent: Failing to utilize employees' skills, talents, and ideas fully can lead to inefficiencies and a lack of innovation.
Benefits of Partnering With a Provider Who Specializes in Lean Manufacturing
Partnering with a lean manufacturing company brings tangible benefits to every aspect of the supply chain. Strategies like reducing setup times, standardizing work processes, and implementing visual management tools can streamline operations, minimize waste, and enhance product quality in facilities, supporting the production of high-quality products at lower costs.
Let’s dive into how choosing a manufacturer that specializes in lean manufacturing can benefit your business.
Cost Savings
Manufacturers can reduce production costs by minimizing waste and streamlining operations, resulting in more competitive pricing for customers. Efficient processes ensure quicker turnaround times and more reliable delivery schedules, enabling better planning and execution. Lean manufacturing also enhances product quality through continuous improvement and defect reduction, ensuring customers receive superior products consistently.
Waste Reduction for Sustainability
Lean manufacturing emphasizes reducing waste at every stage of the production process. This results in minimized material waste, energy consumption, and time inefficiencies. By focusing on lean principles, companies create a more sustainable manufacturing process that benefits the environment and improves the bottom line.
Sustainable practices benefit the environment, enhance the company’s reputation, and appeal to eco-conscious consumers. Customers who prioritize sustainability can align their investments with their environmental goals by choosing products from a lean manufacturer.
Enhanced Product Quality and Customer Satisfaction
One key benefit of implementing lean manufacturing is the significant enhancement in product quality. Companies can deliver products that meet or exceed customer expectations by standardizing processes, identifying and resolving defects early on, and implementing continuous improvement practices. This emphasis on quality not only increases customer satisfaction but also reduces rework and warranty claims, leading to long-term cost savings for all parties.
Customers continuously receive high-quality products that meet their specifications and performance standards. This focus on quality ensures that products are reliable and fit for purpose, reducing the likelihood of defects and returns.
Improved Efficiency and Operational Excellence
Lean manufacturing practices are designed to optimize workflow, enhance communication, and foster a culture of continuous improvement. In manufacturing, this results in increased efficiency, reduced lead times, and improved overall operational excellence.
For customers, this means quicker turnaround times and more reliable delivery schedules. When manufacturers operate efficiently, customers benefit from timely and consistent product availability.
Flexibility and Responsiveness
Lean manufacturing practices make manufacturers more agile and responsive to changing customer demands. This flexibility allows for customized solutions and faster adaptations to market changes. Customers benefit from having their specific needs met promptly, whether it’s through custom designs, sizes, or special features. Lean practices ensure manufacturers can quickly adjust to new requirements, providing tailored solutions that enhance customer satisfaction and efficiently meet market demands.
Increased Customer Satisfaction
By delivering products more efficiently, meeting customer demands promptly, and maintaining high-quality standards, companies can enhance customer satisfaction levels and build long-term relationships. Improved efficiency and quality in production processes lead to better overall customer service. Customers experience fewer issues, timely deliveries, and higher satisfaction levels. A company committed to lean manufacturing will likely have a customer-centric approach, focusing on delivering value and maintaining long-term relationships.
Elevate Your Standards with Vantage Plastics' Lean Manufacturing Processes
Customers can expect high-quality, cost-effective, and sustainable products by choosing a company like Vantage Plastics that utilizes lean manufacturing practices. Lean manufacturing ensures efficient production processes, leading to quicker turnaround times, fewer defects, and reliable delivery schedules. Our commitment to excellence enhances customer satisfaction and fosters long-term relationships.
Contact our team today for more information on how Vantage Plastics implements lean manufacturing and the specific benefits it can bring to your business.