How to Ensure Regulatory Compliance in Thermoformed and Injection Molded Plastics: ISO, FDA, and...
Medical Device Packaging: Ensuring Safety and Sterility
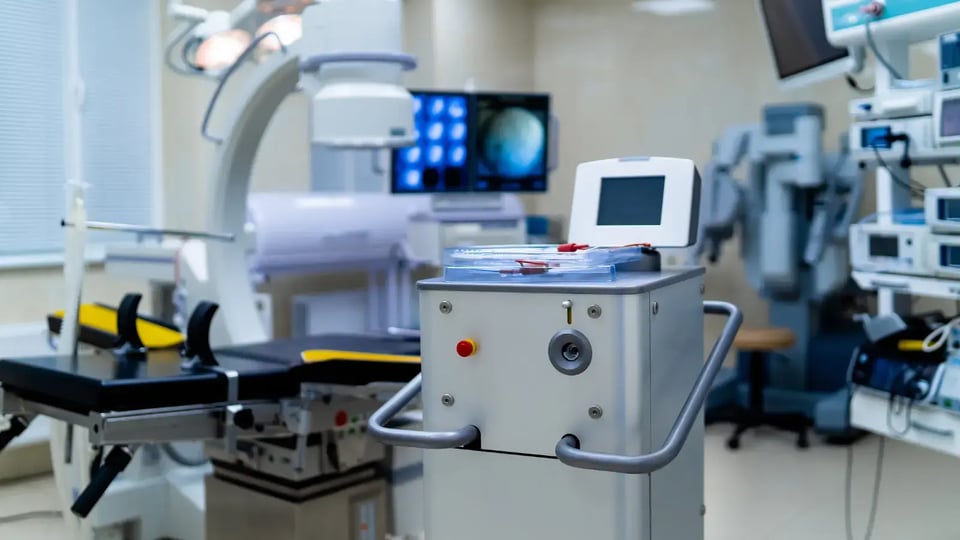
If you're in the medical device manufacturing industry, safety and sterility are a top priority. Many manufacturers rely on two key processes for their medical device packaging: plastic thermoforming and injection molding.
These techniques help create reliable and sterile packaging solutions to ensure products arrive in pristine condition.
The Importance of Medical Device Packaging
Medical device packaging is far more than just a container or wrapper; it plays a crucial role in ensuring that medical devices remain safe and effective. For pharmaceutical giants and medical technology leaders, the packaging process must adhere to stringent regulatory standards to guarantee patient safety and product efficacy.
Imagine a surgical instrument arriving at the hospital only to be contaminated due to inadequate packaging. This could result in severe complications for patients and costly replacements for manufacturers. Why is well-designed packaging for medical devices so crucial?
- Ensuring Product Integrity: Well-designed packaging protects medical devices from physical damage, contamination, and environmental factors during transit and storage. This minimizes the risk of device malfunction, reducing the likelihood of costly recalls and ensuring patient safety.
- Regulatory Compliance: Proper medical device packaging ensures compliance with stringent regulatory standards, avoiding penalties and maintaining the manufacturer’s market access.
- Cost Savings: Effective packaging reduces waste and the need for replacements due to damage. By preventing product loss and ensuring the longevity of medical devices, manufacturers can achieve significant cost savings.
- Enhancing Brand Reputation: High-quality packaging reflects a manufacturer’s commitment to quality and safety. Consistently delivering well-protected products builds trust with healthcare providers and patients, strengthening the manufacturer's reputation and encouraging repeat business.
Plastic Thermoforming in Medical Device Packaging
Plastic thermoforming is a popular method in medical device packaging. It’s a specialized process used to shape plastic sheets into functional and often intricate forms. This technique is widely adopted due to its cost-effectiveness and flexibility, making it a go-to choice for creating reliable, sterile medical packaging solutions.
Applications in Medical Device Packaging
Plastic thermoforming is ideal for various applications in medical device packaging. Its ability to create custom shapes is invaluable for packaging delicate or oddly shaped medical devices. Here are some common uses:
- Blister Packs: These are used for single-use items like syringes, ensuring they remain sterile until use.
- Trays and Clamshells: Perfect for surgical instruments and other reusable devices, these provide a protective shell that maintains sterility and ease of access.
- Custom-Formed Pieces: Custom-formed pieces can be developed for unique medical devices to fit specific shapes and sizes, ensuring maximum protection.
- Pallets and Transportation Packaging: Plastic pallets securely transport large quantities of medical devices, providing maximum stability and protection to ensure safe and intact delivery.
Advantages of Plastic Thermoforming
Plastic thermoforming has numerous benefits for medical device packaging. Here are some key benefits to manufacturers:
- Cost-Effectiveness: Thermoforming is less expensive than alternative production methods regarding tooling and materials.
- Design Flexibility: From intricate shapes to simple trays, thermoforming can accommodate a variety of designs without requiring significant changes to the process.
- Short Lead Times: Due to its straightforward process, thermoforming can yield quicker turnaround times, which is vital in the fast-paced medical industry.
- Material Options: Depending on the packaging's needs, a wide range of thermoplastics, from rigid to flexible, can be used.
Injection Molding for Medical Device Packaging
Injection molding is a critical process in the manufacture of medical device packaging. It is highly efficient and can produce complex shapes with tight tolerances, making it ideal for medical applications.
Applications in Medical Device Packaging
Injection molding has numerous applications in medical device packaging due to its precision and versatility. Here are some specific uses:
- Pill Bottles: Injection molding ensures pill bottles have high-quality sealing surfaces, maintaining medication integrity and safety. The process also allows for child-resistant and tamper-evident closures, enhancing security and functionality.
- Syringe Components: Plungers, barrels, and caps are often made using injection molding to ensure uniformity and precision.
- Vials and Ampoules: These small containers for liquid medications require precise dimensions to ensure proper sealing and sterility.
- Surgical Instrument Trays: Custom-designed trays that hold surgical tools securely in place during transport and sterilization.
- Diagnostic Device Housings: Durable and protective housings for devices like blood glucose monitors and thermometers.
Advantages of Injection Molding
Injection molding offers several key advantages that make it an attractive option for medical device packaging:
- High Precision: This method allows for extremely precise control over the dimensions and shape of the packaging, which is crucial for protecting sensitive medical devices.
- Scalability: Injection molding is highly scalable, making it suitable for both small and large production runs. This versatility is beneficial for manufacturers of all sizes.
- Consistency: The molding process ensures that each part is identical to the last, maintaining the high quality needed for medical applications.
- Material Selection: A wide range of medical-grade plastics can be used, each selected for specific properties such as biocompatibility, strength, and ease of sterilization.
- Efficiency: Once the molds are created, the actual molding process is fast, allowing for high-volume production with minimal waste.
Plastic Thermoforming vs. Injection Molding for Medical Device Packaging
When it comes to medical device packaging, both plastic thermoforming and injection molding offer unique advantages. But which process is best for your products?
Cost Considerations
- Plastic Thermoforming: Generally, thermoforming has lower initial tooling costs. The molds used in thermoforming are less complex and, therefore, cheaper to produce. This makes thermoforming ideal for smaller production runs or when frequent design changes are needed.
- Injection Molding: The initial costs are higher due to the expensive molds required. However, once these molds are made, the cost per unit drops significantly, making it more economical for large production volumes. If you need to produce a high volume of identical items, injection molding can be more cost-effective in the long run.
Design Flexibility
- Plastic Thermoforming: This method excels in creating intricate shapes and custom designs. It's easier to make design adjustments or tweaks without incurring substantial costs. The ability to quickly prototype new designs makes it ideal for custom or less standardized parts.
- Injection Molding: While highly precise, injection molding is less flexible in terms of design changes. Altering the mold can be costly and time-consuming. However, once a design is finalized, injection molding can consistently produce highly complex, detailed parts with exact specifications.
Production Speed and Volume
- Plastic Thermoforming: This process is generally faster for smaller production runs and prototypes. It allows for rapid turnaround times, making it a good choice for projects that need quick delivery.
- Injection Molding: This method shines in large-volume production. Injection molding is highly efficient once the molds are created, allowing for continuous and high-speed production. If you need to produce thousands or even millions of parts, injection molding is often the better choice.
Contact Vantage Plastics to Manufacture Your Medical Device Packaging
Vantage Plastics and LOTIS Technologies, a member of the Vantage Plastics Family of Companies, collaborate to create medical device packaging solutions that ensure safety and sterility from production to distribution. Our experienced teams, with expertise in thermoforming and injection molding, handle various projects with precision. This partnership combines advanced materials, precision manufacturing, and a commitment to quality and sustainability, setting new industry benchmarks.
Medical device manufacturers can rely on our rapid prototyping, stringent quality control, and compliance with medical standards. Our focus on developing eco-friendly materials and optimizing processes underscores their dedication to sustainability. Together, Vantage Plastics and LOTIS Technologies provide innovative, reliable, and high-standard packaging solutions for medical devices. Contact our team today to get started.