What Can Be Made by Thermoforming?
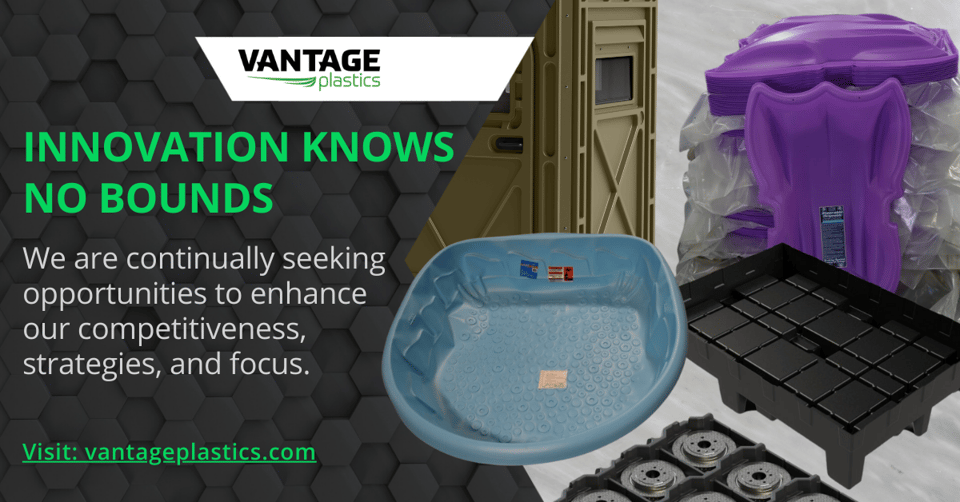
Thermoforming is an efficient and highly customizable manufacturing process that makes everything from food containers to outdoor equipment. But what kinds of things are regularly made by thermoforming?
Thermoforming is a manufacturing process that uses heat and pressure to mold sheets of plastic into almost any shape. Here at Vantage Plastics, we use thermoforming to make parts for all kinds of applications, including those in the agricultural, construction, recreation, and automotive industries.
We often get asked questions about the strengths and limitations of thermoforming. So here’s a quick primer on what you can (and can’t) do with thermoforming.
WHAT CAN BE MADE WITH THERMOFORMING?
The list of things that you can do with thermoforming is almost endless. Some of the things we commonly make are things you’d expect, like pallets, trays, and containers for material handling. But we also use thermoforming to make sleds, outdoor equipment like hunting blinds, porta-johns, kiddie-pools, and agricultural and automotive components.
Currently, about half of Vantage Plastics’ output has to do with containers for transporting products, such as parts that are made in one plant and assembled in another. Agricultural shipping products – like our egg pallets – are also a big part of what we do. But the potential applications for thermoforming are huge.
WHY DOES THERMOFORMING WORK FOR THESE APPLICATIONS?
Thermoforming is a great choice for containers and parts because you can choose the type of material to use; you can really dial in on the properties that will exactly fit the requirements. It’s also very flexible and fast; we can create a prototype tool (usually made of wood) and use that to tweak the design. It’s a very cost-effective way to ensure the form, function, and fit are right. Another major advantage is the robust nature of thermoformed plastic products which gives them a long lifespan allowing for multiple uses. At the end of their useful life, they can also be recycled and made into new products thus allowing for a sustainable future.
Once everything’s good with the prototype, we can quickly cast an aluminum production tool and start making the actual product. There’s actually a lot less overhead with thermoforming in terms of tooling.
Another thing that makes thermoforming a popular choice is how efficient it is with large-scale products. It can be less than half the cost to use thermoforming rather than injection molding in that case.
WHAT SHOULDN’T BE MADE BY THERMOFORMING?
To answer this question, it helps to understand how thermoforming works at a very basic level.
Essentially, a large sheet of heat-softened plastic is draped over a metal tool. The plastic is molded over the tool (usually by atmospheric pressure) and the product takes its shape.
Because of this process, you can’t always get the heated plastic sheet into sharp corners or straight vertical walls. For this, injection molding is usually preferred. The key factor is the shape of the desired object.
THE MOST UNUSUAL THINGS WE’VE THERMOFORMED
One of our most unusual and exciting projects had to do with shipping large solar batteries for a well-known multinational clean energy company. This company had solar batteries that could power all or some of a house, and they needed a way to safely deliver these batteries and install them in people’s houses. While cardboard boxes were one option, they weren’t a very environmentally friendly process; the boxes would be torn down and thrown away every time.
Initially, the company approached us to design some parts that would go inside the cardboard boxes and protect the battery during shipping. But our engineers actually came up with an entire reusable plastic container that completely eliminates the cardboard box. Now, when the crews install the batteries, they simply clean out the battery shipping container and reuse it. Not only has this saved the company a lot of money (millions of dollars in the long run), it’s so much more environmentally friendly. It’s something we’re really proud of.
THERMOFORMING AND THE FUTURE OF PART MANUFACTURING
In conclusion, it’s hard to think of many areas where thermoforming isn’t a great option. There are still an endless number of potential new thermoforming applications to be discovered, and it can really save time and money during the manufacturing process and in most cases provide a tremendous ROI for the customer.