The history of thermoforming plastic is rich and spans over a century, marked by significant...
Thermoforming is Ideal for Medical Equipment
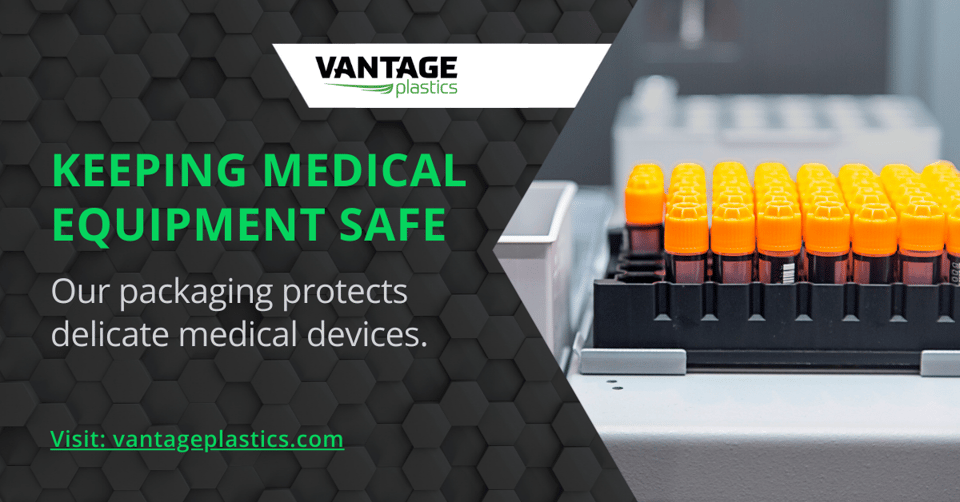
Among the challenges:
- Medical equipment is fragile.
- Medical equipment may contain hazardous materials.
- Medical equipment can be oversized, heavy, and oddly shaped.
- Medical equipment can be expensive.
- In emergencies, medical equipment is in high demand and needs to get to its destination fast.
- Some medical equipment is finely calibrated and needs to stay that way.
- Medical equipment is intended for sterile environments, which means it must be transported cleanly and safely.
In this article, we look at the challenges medical equipment manufacturers face and why thermoforming is the ideal solution for creating customized plastic packing, shipping and storage containers.
MEDICAL EQUIPMENT IS UNLIKE ANY OTHER FREIGHT
Medical equipment is unlike other cargo. Whereas products in industrial industries are often cookie-cutter in design, medical devices come in all shapes and sizes.
What qualifies as medical equipment?
- Lab equipment
- X-ray machines
- MRI machines
- CT scanners
- Surgical devices
- Hospital beds and treatment tables
- Medications and miscellaneous medical supplies
THE CHALLENGES OF SHIPPING MEDICAL EQUIPMENT
Medical equipment logistics requires special expertise. Here’s what makes packing and shipping medical equipment tricky.
- Size. Some medical equipment can be very large in size. Think of MRI machines that fill entire rooms. For shipping, these machines are often transported in sections that need to be safeguarded during travel.
- Shape. Robotic equipment and the lights used in operating rooms have articulating arms that don’t fit into neat packages. This equipment can require custom dunnage that protects it while being shipped.
- Hazardous materials. Some medical equipment includes hazardous materials that must be safeguarded from spilling.
- Fragile. Some medical equipment contains lenses or glass or other brittle materials. These fragile elements must be protected. Some medical equipment must also be kept in calibration during transit.
- Expensive. X-ray and MRI machines cost tens if not hundreds of thousands of dollars. A truckload of them costs many millions of dollars.
- Cleanliness. Equipment intended for hospitals and clinics must be kept clean and sterile.
- Temperature. Some equipment and materials may need to be temperature controlled. Sensitive equipment must not be exposed to extreme temperature changes that could damage instrumentation.
THE BENEFITS OF THERMOFORMING FOR SHIPPING MEDICAL EQUIPMENT
Plastic, like that used in thermoforming, offers the following benefits for shipping medical equipment.
- Plastic is customizable. It can be formed into virtually any shape.
- Plastic is lightweight. Compared to wood, plastic is much lighter.
- Plastic is reusable and recyclable. Plastic pallets and custom designed trays or containers can be used again and again hundreds of times.
- Plastic is clean. Compared to wood, which may contain insects or bacteria, plastic is cleaner and can be washed and sterilized.
5 QUESTIONS MEDICAL EQUIPMENT MAKERS SHOULD ASK
Here are five questions medical equipment makers should ask about their packing and shipping:
- How customizable are your shipping containers? Thermoform molds can be built in any configuration.
- How sterile are your shipping containers? Wooden pallets are dirty. One study found that 12% of wooden pallets contain harmful bacterias such as listeria, along with other contaminants like petrochemicals.
- How protective are your shipping containers? Thermoformed containers can be molded and shaped to hold medical devices securely to eliminate movement during transit.
- What is the return on investment of your shipping containers? Wooden pallets are used once. Plastic can be reused and recycled. Reference Edge Materials Management.
- How light are your shipping containers? Plastic pallets and packaging are lighter than their wooden counterparts, which helps reduce the amount of fuel needed to ship them.
HOW SMART PACKAGING FROM VANTAGE PLASTICS HELPS MEDICAL EQUIPMENT MANUFACTURERS
As members of the Reusable Packaging Association, Vantage Plastics adheres to the tenets of Smart Packaging. Smart Packaging seeks to reduce cost and improve efficiency of packaging, not only by using reusable materials but also by adopting smart processes.
Smart Packaging aims to improve shipping by improving:
- Protection. Keeping products safe and secure.
- Density. Allowing more products to be shipped in each load.
- Weight. Reducing the weight of packaging to improve fuel economy.
- Ergonomics. Improving the design of packaging to make it easy to handle and less prone to breakage.
- Automation. There is a growing need for packaging design that can interface with automation.
- Sustainability. Developing a circular economy with reusable and recyclable packaging helps fulfill green initiatives.
- ROI. Return on investment is more complex than only considering front in cost. Old methods need to be reconsidered.
Plastic outperforms wood in all these aspects.
CHOOSE VANTAGE PLASTICS FOR MEDICAL EQUIPMENT SHIPPING
If you are a manufacturer of medical equipment or supplies, contact Vantage Plastics for your packing and shipping needs. We can create customized dunnage and containers that keep your equipment safe, clean, and protected.